Spotlight Feature
Best Practices for Packaging Line Optimization
Experts share tips and ideas on taking your packaging line to the next level.

Optimizing a packaging line is a journey. And there are many variables to consider in the quest. If one machine or component isn’t working, it can wreak havoc on your entire line — with labor costs, downtime and of course finding the root of the issue. Throw automation into the mix and there are even more variables.
Optimization takes many forms — whether it involves taking what you have available and making it better or upgrading an operation with superior equipment. It may include looking at floor space, downtime, throughput, energy, total cost of ownership, return on investment, waste, employee training and so forth.
Here, six packaging experts offer tips and best practices for packaging line optimization, as well as advice on starting from scratch. They are: Michael Graf, director of consulting at Schubert-Consulting, a unit of Schubert Packaging Systems GmbH; Anurag Mitra, product marketing manager at tna solutions; Dache Davidson, vice president of marketing at Pregis; Anand Bhasi Rajan, sales head for ACG Engineering (part of ACG Group); Marc Wolf, general manager and vice president of Matrix (a ProMach brand); and Paul Moore, vice president of sales at PMI Kyoto.
What tips do you have to share on how to optimize a packaging line?
Graf: You need a holistic view of the line instead of focusing on a single component — this is the key. Talk with the operators first to capture their opinion in organization, followed by talks with maintenance staff as well as the operation planning department. In the second stage, ensure that there will be an understanding of all functions to follow, and which machine will be responsible for them. Not only should the machines be evaluated, but keep in mind the packaging material specification of the early start of the machine and the design parameters on the starting point as well. A proper data capturing process followed by root cause analysis will support quick wins during the optimization process and develop trust between the team carrying out optimization and the production members.

Mitra: One of the key requirements for an efficient production line is communication. Line integration is the first step toward operational efficiency, as it ensures that each component communicates effectively with the others. Stand-alone machines from different suppliers that are only connected mechanically through conveyors are often unable to operate at their optimum levels, reducing the overall efficiency of the line. Furthermore, a lot of machines employ different software, making it difficult to evaluate reports and run detailed diagnostics, thereby limiting the ability of operators to effectively monitor any unusual activities and react quickly.
Davidson: We believe that doing a full packaging line audit up front is the only way to truly understand what is and isn’t working for an operation. We also review all ergonomic factors to optimize the workstation configuration for packers to reduce non-productive movement, maximize uptime and keep packages moving through the fulfillment process at optimal speed for the operation.
Wolf: To best optimize your packaging line first requires a thorough understanding of all the components within your line. The key to a successful packaging line that meets your production and sales goals is to know what’s happening before product arrives, as well as its destination after it’s been packaged.

Rajan: We strongly believe that standardization is the key to a successful project. Using standardized prequalified designs ensures the shortest lead time for delivery, significantly reduces risk, improves documentation quality and overall equipment reliability and performance.
Moore: Companies want easy to operate, consistent machines in a packaging line. Large companies invest heavily in developing exhaustive bid specifications that cover everything from HMI design to specifying components and wire sizes. Small and mid-sized companies can achieve the same benefits for a fraction of the cost by picking one company to supply multiple pieces of equipment, instead of selecting a different machine supplier for each machine.
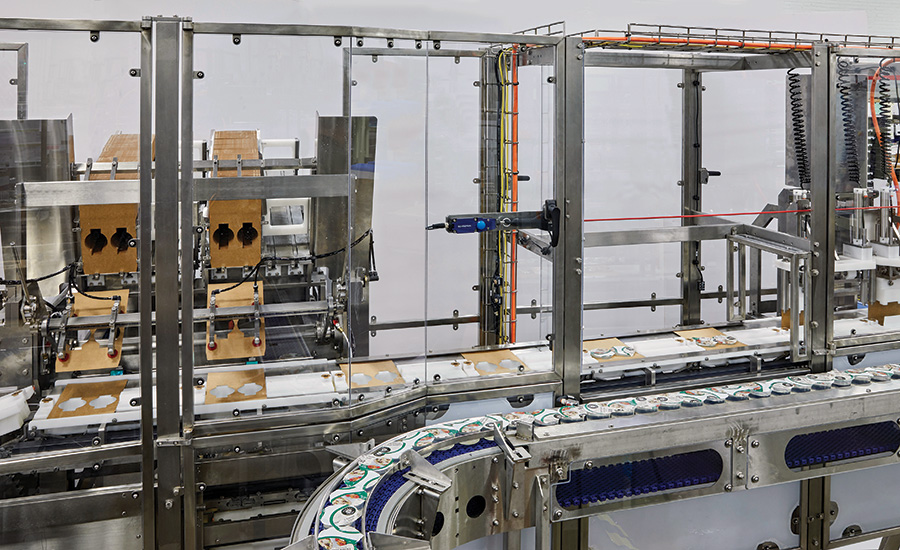
How about specific variables like speed, cost, downtime, automation, compact floor space?
Graf: Soft factors and their effects to the OEE are essential to be considered in the optimization work. The mindset of people involved in the production process is part of analysis as well. Skill set and training availability will support production increase when helping hands are available at the right time at the right place. Purchasing departments are often an essential part of the production, due to their decision on which kind of packaging material is purchased and how the material will be delivered to the line.
Mitra: As production lines become more automated, products are now processed at unprecedented speeds, increasing the chances of damage or breakage. Often caused by inaccurate control equipment or badly tuned processes, material waste is a real problem for any plant manager and can affect the entire production cycle. If unnoticed, just one fault could cause considerable bottlenecks, resulting in unnecessary downtime and excessive wastage. With a detailed user requirement specification (URS), control system providers can help identify the required key performance indicators (KPIs) that a particular manufacturing process requires. As well, power saver software with features such as ‘stand by time’ can significantly lower a plant’s energy usage and carbon footprint.

Davidson: We look at all aspects of the packaging operation before recommending an optimum solution. This includes material, equipment, labor, energy, speed, safety, postage, damage rate, etc.
Rajan: Our recent introduction of the NXT line incorporates a high level of automation, and with a focus on Industry 4.0 connectivity and smart manufacturing prowess. Each of these elements should be considered when selecting a packaging line supplier, since each element contributes to the overall Operating Equipment Efficiency (OEE) and Total Cost of Ownership (TCO).

Moore: Allow your equipment suppliers to help you increase machine efficiency. This means understanding how to use the error logging that leading machine suppliers build into their HMIs. When the same error arises twice, take videos of the troubled area and share with the machine supplier.
Any other advice to those looking to put a line in place?
Graf: Keep a closer look at the amount of change and format parts at your line. The more standardization of products and packaging you might achieve, the less changeovers of the line are required and the more productive time is available and as a result, the OEE will increase. Training in virtual reality allows the line to produce, and people getting trained on the virtual twin of the line prepared for reality. Production no longer needs to be stopped for training purpose and therefore, the production output will be there during training.
Mitra: The top three advice points we would give are: 1. When optimizing a packaging line, clearly establish what challenges you’re looking to overcome; 2. As consumer trends evolve, so will packaging requirements. Any new packaging line implemented must allow manufacturers to adapt to changing consumer needs effectively and efficiently. Be sure to select equipment that offers the ultimate in flexibility; 3. Setting clear and measurable KPIs that the new packaging line should help achieve is crucial to evaluate its performance over time.
Davidson: Make sure that you are evaluating the packaging materials and equipment early in the process.

Wolf: The means to achieving a high rate of efficiency in your packaging line is selecting the right equipment and supplier for your specific application. A best practice is to always do your homework and look at the track record of different suppliers.
Rajan: Our principle focus would be for the customer to leverage current and upcoming technology. Digital technologies, such as IoT, artificial intelligence and augmented reality, are now being used widely across industries and, for packaging equipment, will soon be the norm rather than the exception. The ROI for such investments is swift, and the long-term savings are phenomenal. We would also advise our customers to look at technological solutions like predictive maintenance and proactive servicing, both of which help maximize their machines’ OEE and productivity.
Moore: If you’re considering purchasing a packaging machine that is not built in the U.S., be sure to do a thorough investigation of parts availability and cost. Also see if the builder can demonstrate the ability to modify the machine here in the U.S. (just in case it needs to be repurposed later in life).
Top 10 Best Practices There is a lot of information and good nuggets to take from the answers above. Here is a simple breakdown from the Q & A:
|
Looking for a reprint of this article?
From high-res PDFs to custom plaques, order your copy today!