Bosch Rexroth Introduces Smart Flex Effector
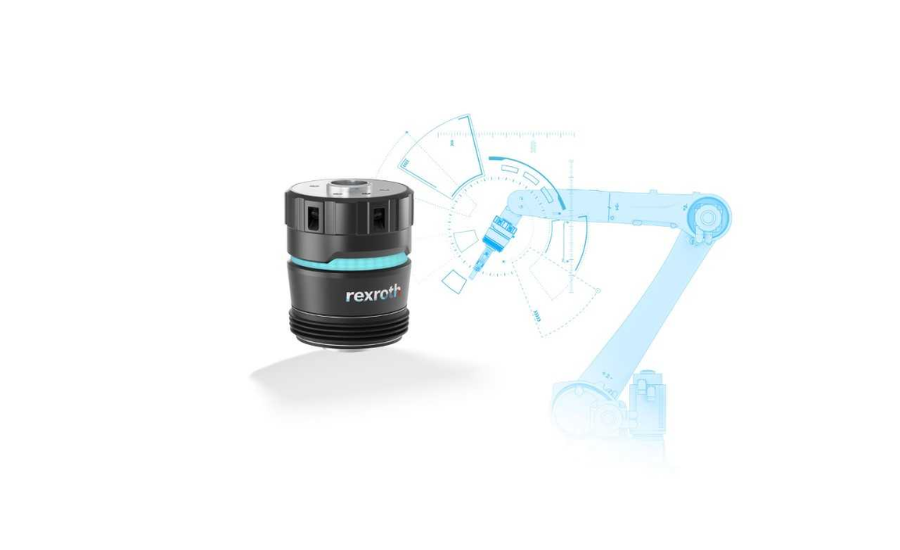
Bosch Rexroth, one of the world’s leading suppliers of drive and control technologies, has announced the release of the Smart Flex Effector, a new, sensor-based compensation module that gives robots and Cartesian linear systems human-like sensitivity, giving way to new opportunities for factory automation. Thanks to an innovative kinematics system that works independently in six degrees of freedom, processes that were once difficult to manage can now be automated with limited error and maximized efficiency.
Designed for handling loads of up to 6 kg, the Smart Flex Effector opens up a wide range of new functions which were difficult or impossible to implement with previous equipment, such as passive compensation units, force torque sensors and visual systems. The applications range from process automation and quality monitoring to teaching and the controlled handling of objects.
The teaching process for the Smart Flex Effector is incredibly simple, as the robotic control system can read the exact coordinates for gripping and placing points directly, and it can also be taught manually by moving it into the correct position by hand. Thanks to its tactile sensitivity, the Smart Flex Effector is also able to complete processes with great complexity and tight tolerances, while also being able to properly handle fragile materials.
The Smart Flex Effector also allows for improved quality thanks to a transparent process that makes documentation of errors easier, as deviations are recognized immediately and either corrected or reported to the control system, leading to a reduction in follow-up work.
In addition to its other benefits, installation is extremely easy, as the Smart Flex Effector is simply screwed to the robot flange and the gripper, and the locking function and data transmission are available as soon as the unit is connected to the power supply and the control system.
To learn more about the Smart Flex Effector, please visit www.boschrexroth.com/en/us/smart-mechatronix/smart-flex-effector.
Looking for a reprint of this article?
From high-res PDFs to custom plaques, order your copy today!