Plastics Company Announces All Facilities to be Certified by the Global Food Safety Initiative
The company is one of the industry’s first plastics packaging suppliers to gain GFSI certification.
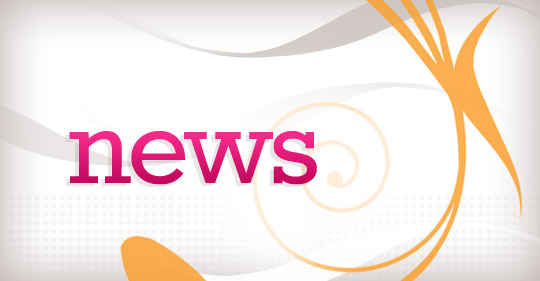
Amcor Rigid Plastics, one of the world’s leading producers of rigid plastic packaging, has announced that all manufacturing facilities have earned or will earn certification by the Global Food Safety Initiative (GFSI), a global retailer-driven program that seeks continuous improvement of food safety management systems to ensure confidence in the delivery of safe food to consumers worldwide.
Amcor has desired to take a leadership role in GFSI certification and is one of the industry’s first plastics packaging suppliers to gain certification, according to Tod F. Eberle, Amcor’s vice president, Quality Systems, Engineering Standards, and Advanced New Platform Technologies. As part of this customer-driven initiative, the company has certified 27 of its North American manufacturing facilities, and three remaining newly acquired or greenfield plants are expected to be certified this fiscal year. Amcor undertook the effort in 2010 and expects all 60 of its production facilities in the Americas to be GFSI certified in early 2014.
“As the world’s largest plastics packaging supplier, we clearly understood the value of adapting our existing highly functional Amcor Quality System to the requirements of GFSI,” explains Eberle. “Already recognized for our state-of-the-art quality and safety systems, our intention was to enhance our position to meet the most stringent global standards ahead of the market, helping to ensure the quality and safety of products at the retail level.”
GFSI provides a platform for collaboration between some of the world's leading food safety experts including retailers, manufacturers, food service companies, service providers associated with the food supply chain, international organizations, academia and government. GFSI is overseen by the Consumer Goods Forum, a global consortium of the world’s leading food and beverage companies and retailers including Coca-Cola, Kraft, PepsiCo, Ocean Spray, Nestle, Danone, and Wal-Mart.
Previously, food safety audits varied significantly across the world and there were no existing audit systems that could be qualified as “global” and could be adopted by all suppliers, explains Eberle. For example, Amcor’s quality and product safety program utilized an audit system that wasn’t benchmarked across regions. Implementing a global system which has been designed with the next level of food safety in mind is meant to further demonstrates Amcor’s commitment to innovation in all aspects of its manufacturing development and quality processes.
GFSI implemented standardized definitions, benchmarking guidelines and food safety systems, and developed a model for companies to follow to become certified internationally, according to Eberle. Amcor played a direct role in the development of the packaging standards and provided input and expertise in the creation of the GFSI Guidance Document.
The GFSI initiative was launched in 2000 following a number of food safety crises when consumer confidence was at an all-time low. Since then, experts have been collaborating in numerous Technical Working Groups to tackle current food safety issues defined by GFSI stakeholders. GFSI has worked to achieve harmonization of food safety standards to help reduce audit duplication throughout the supply chain.
Amcor plants have been certified under Food Safety System Certification 22000 (FSSC 22000 as extended to Packaging Manufacture by PAS223). Plants must comply with Good Manufacturing Practices (GMP) and Hazard Analysis Critical Control Points (HACCP) regulations. Surveillance audits are done annually and recertification is required every three years.
Looking for a reprint of this article?
From high-res PDFs to custom plaques, order your copy today!