Machinery Technology: Robotics & Automation
Rise of the packaging robots
Automation is pushing the boundaries of technology to new levels of success.
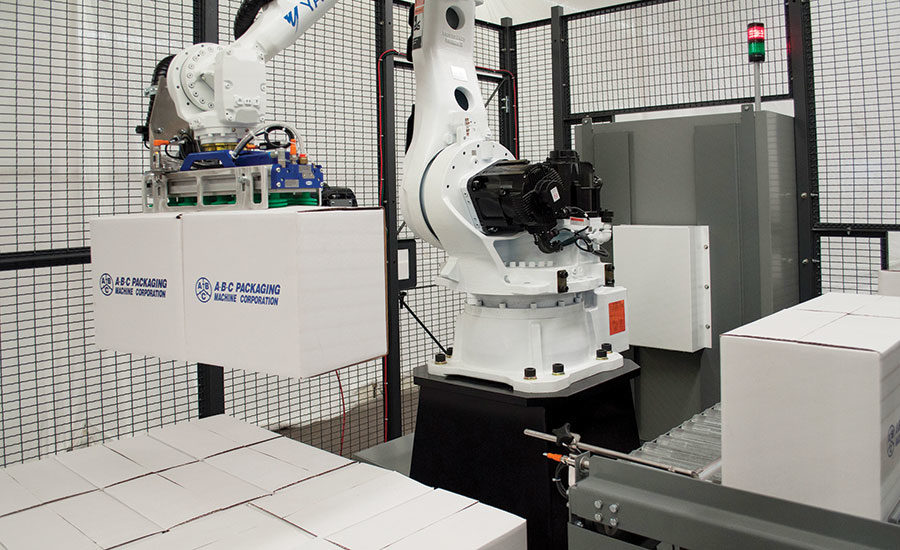
The new 700 series robotic palletizers from A-B-C Packaging offer the flexibility of manual palletizing with reduced costs and liability.

CSB Automation’s IT solution fully automated a Dutch manufacturer’s in-house logistics.

ESS Technologies integrated the FANUC CR35iA Collaborative Robot, with 24 sensors that stop all motion when in contact with an object or person.



The robotics market in North America set new records for the first nine months of 2016. According to the Robotic Industries Association (robotics.org), 23,985 robots, valued at $1.3 billion, were ordered from North American companies in the first nine months of 2016 – an increase of 7% in units over the same period in 2015.
“It’s a great time to get involved with robotics,” says Jeff Burnstein, president of RIA. “Today’s robotics industry offers innovative products, fulfilling employment opportunities and competitive advantages for a wide variety of companies.”
And many agree. Our monthly online poll asked: Why choose robotics and automation for your packaging line? Forty-eight percent of voters said that increased speed and reliability, to replace human workers and sanitation/safety concerns were all factors in their choice. The top single choice was increased speed at 33%, followed by sanitation and safety at 12%. Following are just a few recently launched robotic and automation machines that tout these line benefits.
A-B-C Packaging (abcpackaging.com) introduces the new 700 series robotic palletizers, designed to deliver the flexibility of manual palletizing with reduced costs and liability, as they automatically accumulate and stack cases, trays, bags or shrink-wrapped multipacks in multiple configurations and pallet loads. Packagers looking to save on floor space and ship secure, well-formed pallet loads made to protect products throughout distribution might want to try the 700 series.
700 series standard systems include a high payload robot and product handling devices for single or dual infeed and pallet building, product transport and staging conveyors, high visibility guarding, Allen Bradley controls and programming for product requirements.
Additional pallet patterns can be programmed by the end user and uploaded at the operator panel. The pallet programming software automatically sets the most efficient arm movement to maximize palletizing speed. A variety of end-of-arm tools are available to accommodate all product types.
Another innovator, ESS Technologies (esstechnologies.com) has integrated FANUC America’s CR35iA Collaborative Robot. It features 24 precision sensors that stop motion when in contact with an object or person. Since it’s designed to operate in close proximity to humans in a shared workspace, there is no need for safety fences. It can also reduce the robotic cell footprint.
The CR35iA offers a payload of 35kg and a reach of 1,811mm. The green robot cover is padded to reduce impact forces pinch points by providing a barrier between a human operator and a robot arm. ESS designs the robot end-of-arm tooling (EOAT) to pick and place cases in a pre-programmed pattern.
When integrated with serialization track-and-trace systems, the CR35iA can be programmed to hold case labels over cameras or barcode scanners to verify pallet load or supply automatic reject of incorrectly labeled cases.
An IT solution from CSB-Automation and CSB-System (csb-system.com) is helping a Dutch manufacturer of prepacked meat with automating its in-house logistics. ProMessa’s entire materials flow has been automated with the CSB solution – from packaging following production, to storage and picking, and loading onto trucks.
ProMessa is using the software to organize and monitor a network of machines, including two automatic crate storages, robot units, four automatic weigh labeling lines with connected sorters, a dispatch warehouse and a conveyor system. The IT solution also integrates production scheduling to ensure precise tuning of workflows in terms of time and quantity. Details like up-to-date order, production and inventory data are captured and processed in real time. This degree of networking promotes fast, error-free processes and greater productivity.
The intralogistics system was designed to offer a high level of productivity and flexibility. The result – ProMessa’s delivery performance is currently over 99%.
We asked Mark Cox, director of technical training and advanced systems at Advanced Technology Services (ATS; advancedtech.com) how PdM is changing the industry and what the future looks like for robotics and automation. Packaging Strategies: What is PdM? Cox: Predictive Maintenance (PdM) is the gathering of information by various means to predict when a failure might occur and prevent or delay that failure by performing maintenance before the failure can occur. PdM is much easier defined than successfully executed in today’s manufacturing environment. In many cases, the real road block to the success of these strategies is the actuality that companies don’t use the information gathered to improve. Another misnomer that delays or impairs a PdM program is the perceived difficulty, expense and time required for “gathering information.” Included within many industry definitions are references to technologies like vibration analysis, oil analysis and thermal imaging. I also see references to concepts and systems like condition-based monitoring, sensors, CPAS and wireless communication networks – all valid technologies and concepts that are often required to get to the Holy Grail of zero maintenance-related down time. But consider the reality that eyes, ears and feel can provide more than enough information to foster a basic, yet successful PdM program. PS: How will implementation of PdM and robotics lower costs/ Cox: A robust PdM program can have a significant impact in reducing the manufacturing cost of product. As an example, I don’t believe anyone would argue that a well-maintained machine tool or process line will produce a more quality product over time than a poorly maintained one. It’s just a fact that less reactive maintenance as a result of a robust PdM program equates to lower overall maintenance cost, more available production hours and lower costs in spare parts and supplies. Significant increases in productivity can also be gained with the implementation or upgrading of existing technologies such as robotics. Beyond the fact that robots don’t take breaks or call in sick, they are incredibly reliable and resilient pieces of equipment. For example, manufacturer of robotic equipment, FANUC is currently reporting mean time between failures rates in excess of 100,000 hours. That’s more than 10 years of continuous operation without a failure. Of course many factors can impact those rates, including how robust a company’s maintenance program truly is. But it’s remarkable the abuse today’s robotic technology can absorb without impacting production availability. PS: Is anything in particular standing out in the market? Cox: Robotic manufactures are continually pushing the boundaries of technology. Today’s robots are incredibly fast – in some pick and place applications, robots can achieve 120 cycles per minute or more. Integrated scanners and their ever-increasing ability to react to a multitude of variables in the blink of an eye are continually expanding the value robots bring to processes such as order fulfillment, palletizing, de-palletizing and packaging. Huge gains in the area of collaborative robotics and their ability to work jointly with production workers are becoming more common place in the industry. In the past, safety concerns limited collaborative opportunities. Today’s embedded technologies combined with sensors, scanners, dual check safety and advanced control systems have all but eliminated those concerns. One of the most exciting trends in robotics today is in some of the OEM’s efforts to achieve zero downtime. Robots predicting failures weeks in advance, checking OEM stock, shipping a replacement part to the end user and preparing the work order is reality. I remember when we celebrated a robot actually running a complete shift. Those days are gone forever. |
Looking for a reprint of this article?
From high-res PDFs to custom plaques, order your copy today!