Supplier insights
Minimizing waste in your packaging line
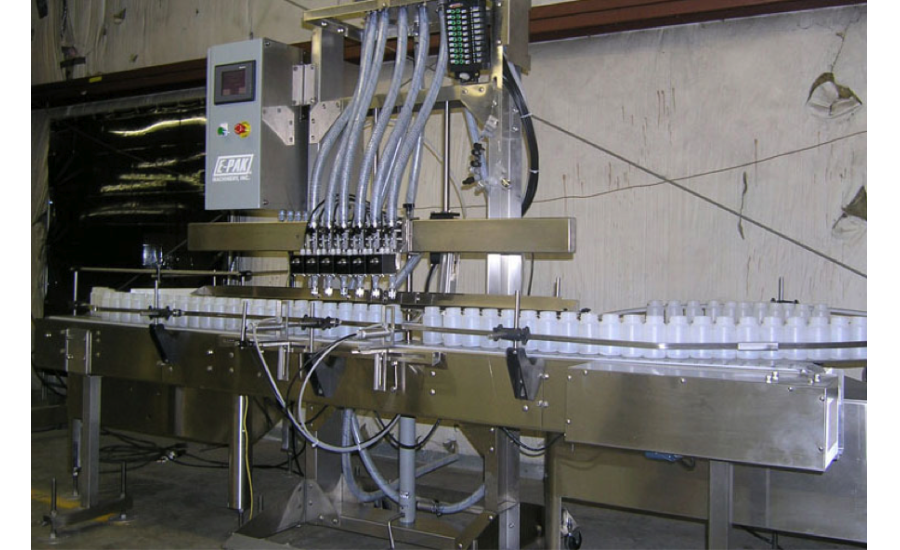
One of the most common ways businesses lose profits in liquid packaging lines is through wasted product. Waste is particularly problematic with older liquid packaging equipment, which is why it's necessary to make sure that your production line uses consistently reliable machinery.
Liquid products consist of varying viscosities, which means that specific types of liquid filling machines are needed to fill certain products with consistent accuracy and efficiency. Today's liquid fillers and other packaging machines are more efficient than they've ever been, and a combination of them can help eliminate product waste and maximize profitability.
Use liquid fillers to accurately fill liquid products
Reliable liquid fillers are available for many different types of liquid products. It's important to make sure your production line utilizes the equipment that can handle your product. There are many different types of liquid fillers that a packaging line can utilize, each with different features for a wide range of applications.
Some of the different liquid fillers include:
Gravity fillers
Both gravity and pressure/gravity fillers are capable of bottling nearly any type of water-thin to medium-viscosity liquid product. However, gravity fillers are more ideal for thinner and foamy liquids, while gravity/pressure fillers are useful for filling thicker products.
Net weigh fillers
Net weigh fillers are great for filling products in bulk quantities without leaving any wasted product, ensuring that each container contains the same amount of product.
Overflow fillers
These automatic or semi-automatic filling machines can fill many low-viscosity or water-thin liquids into a wide range of containers at a consistent cosmetic level.
Volumetric piston fillers
These liquid filling machines can fill liquids ranging from water-thin to thick and chunky.
Molten product fillers
Some liquid products are particularly thick and require heating to fill them in containers. Molten product fillers can fill products such as candles, petroleum jelly, shoe polish, lip balm, and many other types of molten products.
A combination of these machines can give your production line what it needs to avoid product waste, with features such as anti-drip and anti-foam nozzles in addition to consistent fill levels for every container.
Other types of liquid packaging machines
While liquid fillers that fill containers with maximized accuracy and efficiency, the other machines in your production line need to be able to further prevent product wastage.
Apart from product wastage during the filling process, certain other factors such as contamination and spillage can result in lost product, requiring machinery that can prevent it. There are several main types of machines that you should use to avoid wasting products and keep your packaging line productive from start to finish.
Conveyors
As your liquid products travel down the line, conveyors are responsible for making sure they get where they need to go throughout the entire packaging process. Today's conveyor systems are designed to keep products moving at consistent speeds while providing enough traction to prevent products from spilling.
Bottle cleaners
Prior to filling containers with liquid, production lines should utilize bottle cleaners to remove all dust particles and other potential contaminants. Any amount of contaminants that exceeds FDA limits will result in wasted product.
Have fully trained operators
The machinery in your production line can only do so much to eliminate product wastage. If you want your systems to function properly and avoid malfunctions that result in product loss, you need to make sure your staff can effectively handle and manage all of the equipment in your facility.
All machine operators should understand how each piece of equipment operates and help ensure that they maintain optimal performance. The best way to ensure your staff can effectively manage the production line is to enforce mandatory training for each operator.
With properly trained staff in control of your packaging systems, you'll remain comfortable in knowing that your product is in good hands, with minimal wastage.
Combine people and equipment in your facility to eliminate the risk of product waste
A complete system of equipment specifically designed and configured for your product can significantly decrease the chances of product wastage, and trained operators will be able to further reduce this risk.
With fully optimized machinery and attentive staff behind your operations throughout the entire packaging process, you'll be able to effectively avoid contamination, breakdowns, spillage, or malfunctions that could result in wasted products and lost money.
Looking for a reprint of this article?
From high-res PDFs to custom plaques, order your copy today!