Omron’s Sysmac Delta Robot Series increases production in high-speed pick & place packaging
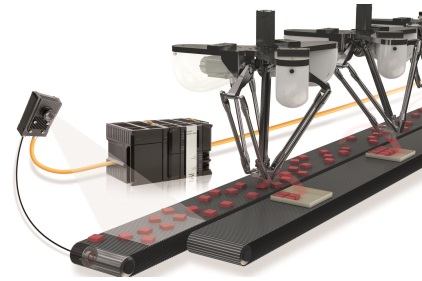
Omron Automation and Safety offers the Sysmac Delta Robot Series to help machine builders add efficient pick-and-place capability to packaging and small parts assembly line projects. Omron’s integrated Sysmac robotics solution offers the capability to integrate machine control, motion, remote I/O, HMI, safety, vision and robotics all in one controller, over one network, using one programming software.
Sysmac Delta robot-centered solutions allow operators to increase production capabilities to new levels by building higher through-put machines that can handle more than 100 picking operations per minute. The Delta Robot solution can achieve up to 200 cycles per minute, and can be synchronized with multiple conveyors to perform on-the-fly Pick & Place operations. There are currently four robot sizes available: Standard Delta, Extended Reach Delta, Washdown Delta and Mini Delta robot.
The Sysmac Delta Robot Series operates on a Sysmac-NJ Controller – Omron’s all-in-one platform that integrates robotic, motion and sequential logic control into a single multitasking controller. Utilizing the EtherCAT motion network, the NJ controller delivers maximum speed, accuracy and predictability.
Other key features of the Sysmac Delta Robot Series include:
• Control of up to 8 robots by one NJ controller
• Number of axes: 3 + 1 optional rotational axis
• Up to 200 cycles per minute
• Reach range: from 450 (Mini) to 1300 mm (Extended Reach, Washdown)
• Payload range: 1 to 3 kg
• IP class range: IP65, IP67 hygienic design
• EtherCAT & EtherNet/IP Connectivity standard in NJ Controller
• Control each axis with G5 Series Servo Drives to complete the system
Looking for a reprint of this article?
From high-res PDFs to custom plaques, order your copy today!