Smaller, faster, more practical stretch hood machine debuts
BEUMER has developed a new machine from the BEUMER stretch hood model range.
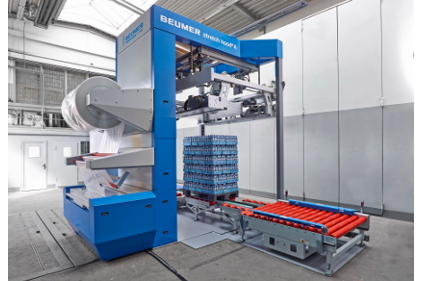
As a single-source provider for filling, palletizing and packaging technologies, BEUMER Group (beumergroup.com) supports its customers in all respects supplying sustainable solutions from a single source.The BEUMER stretch hood A sees the intralogistics specialist from Beckum redesign its tried-and-trusted packaging system from scratch. During the development, our specialists analysed various components and optimised them in terms of function, arrangement and ergonomics. This includes an intuitive menu system on the machine control via a soft-touch panel, an optimised, ergonomically designed workplace for the operator and material-friendly transporting of the film in the machine thanks to an innovative film transport system. The new system also features improved system performance and needs far less floor space.
For companies in the construction material, chemical or food and beverage industries, the topic of safety when transporting and storing palletised products has been becoming more important. This is what prompted BEUMER to develop a new machine in its proven BEUMER stretch hood model range that offers even more practical and safer handling for the user, compared with other machines in this model range. To facilitate work for maintenance staff, and thus ensure higher machine availability, the new BEUMER stretch hood A is accessable without a platform and steps.Maintenance work, such as changing the blades, or the sealing bars, are now handled at floor level. The operator opens a drawer for these activities, providing free access to blades and sealing bars. The machine is automatically brought to a standstill to protect the operator. This removes the need to move subassemblies to maintenance position. Due to this rapid access capability, maintenance work is accelerated, and the risk of accidents and malfunctions minimised.
The machine's ergonomics have also been consistently advanced. With just a few actions, and completely without tools, the operator can feed in the film. This means substantial reductions to tooling and conversion times.
Additional benefits include the compact design of the BEUMER stretch hood and the resulting low height and small footprint.
An innovative, material friendly film transport system feeds the previously created film hood into the system. On its way to the crimping and stretching unit, the sealing seam on the film hood cools down so that it can be crimped without loosing time. This removes the need for an energy-intensive cooling unit and time-consuming cooling. The pallets can be packed in a shorter cycle time thus reducing idle times, while at the same time ensuring improved packaging performance and less energy consumption.
The developers have also improved the human-machine interface to offer an even more ergonomic workflow to the user.For this, the intralogistics specialist has introduced the BEUMER Group Human Machine Interface (HMI), a newly-developed operator panel with an optimised user interface and graphical navigation. This easily understandable and intuitive interaction concept helps to define efficient working sequences. The operator can control the machine safely with only a little training saving time and money, which ensures high economic efficiency. The soft-touch panel uses pictograms to guide the user through the machine control menus. The panel also gives the operator access to all required training programs. The system is controlled by a Siemens SIMATIC S7-300.
Energy-saving motors and low compressed air requirements ensure a favourable energy balance. The compressed air requirements have been significantly reduced compared with the previous model.
With its U-shaped frame design, the BEUMER stretch hood can be easily connected to existing conveying systems. Removing the need to interrupt the conveying system also guarantees smooth conveying performance for the pallets and stability of the palletized goods.
Looking for a reprint of this article?
From high-res PDFs to custom plaques, order your copy today!