Simplimatic automation introduces cap feeder to accommodate lighter-weight caps
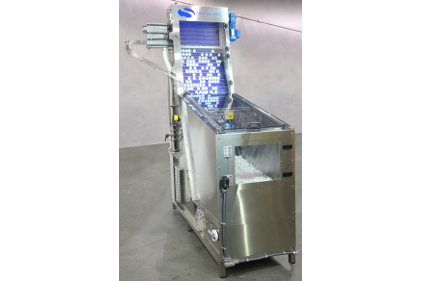
Simplimatic Automation (www.simplimatic.com), a leading provider of conveyors and automation for the semiconductor, electronics, packaging, assembly, pharmaceutical and automotive industries, has developed a new cap feeder that can save time and money by reducing or eliminating the downtime required for retooling to today’s popular, lightweight PCO 1880 bottle caps. The new Simplimatic Cap Feeder Model 1900 incorporates new features that reduce or eliminate the need for change parts, allow simple modification of the hopper size in the field, and eliminate reliance on factory-compressed air.
The new machine is unique in its ability to run different cap sizes of similar styles on the same machine without the need for belt, cleat or hopper modification parts in most cases. Older cap feeders require an on-site technician visit to install change parts when customers need to run lighter-weight caps, resulting in a costly, 16 to 20-hour retrofit.
The new cap feeder can be adjusted while the machine is running, shortening the changeover time from 16 to 20 hours to a little as 15 minutes. Customers can expand hopper capacity from 20 cubic feet to 30 or 40 cubic feet without the need for special tools or the expertise of factory technicians.
The equipment’s rate is based on the largest cap size. Based on a 28 millimeters beverage cap, for example, the cap feeder can achieve speeds of up to 1,800 cpm. Using an internally generated air supply from a concealed blower system, the cap feeder eliminates the need for factory-compressed air in the cap escapement process.
Other standard features include:
- Stainless-steel washdown construction
- Lexan® bin and elevator covers
- Hopper baffle adjustment lever
- Stainless-steel adjustable footpads
- Stainless-steel air piping manifolds
- Left or right-hand discharge
Options include HEPA air filtration, an ionized air de-dusting device, 30 and 40-cubic-foot bin sizes, a stack light system and a jam detect system.
Looking for a reprint of this article?
From high-res PDFs to custom plaques, order your copy today!