Conveyors
Hygienic Improvements with Conveyors Allow Streamlined Packaging Process
Embracing efficiency

Rotzinger’s hygienic conveyor allows for easy cleaning. Courtesy of Rotzinger Group
As the packaging process becomes increasingly automated, a key area of focus for suppliers has been conveyors. Suitable for nearly every packaging sector, conveyors have become more popular due to their versatility and general ease of use. Perhaps one challenge when it comes to fully implementing conveyors, though, is hygiene, as maintaining sanitary conditions is a difficult and often time-consuming process. That being said, several companies are taking steps to mitigate this issue.
- Key Technology’s new conveying systems for robotic pick-and-place packaging are highly automated, which limits the need for hand-packing, which can often be unsanitary.
- Rotzinger Group’s hygienic conveyor features a unique design that limits the amount of residue left on the belt, thus allowing for easier cleaning processes.
- Cablevey developed a “smart cart” that makes the cleaning of tubular drag conveyors much more efficient.
- And finally, Dorner and Garvey developed the AquaGard GT, a conveyor system that is primarily made of stainless steel and FDA-approved plastics.
Read more about all these innovations in conveyors below.
Key Technology Introduces New Conveying Systems for Robotic Pick-and-Place Packaging
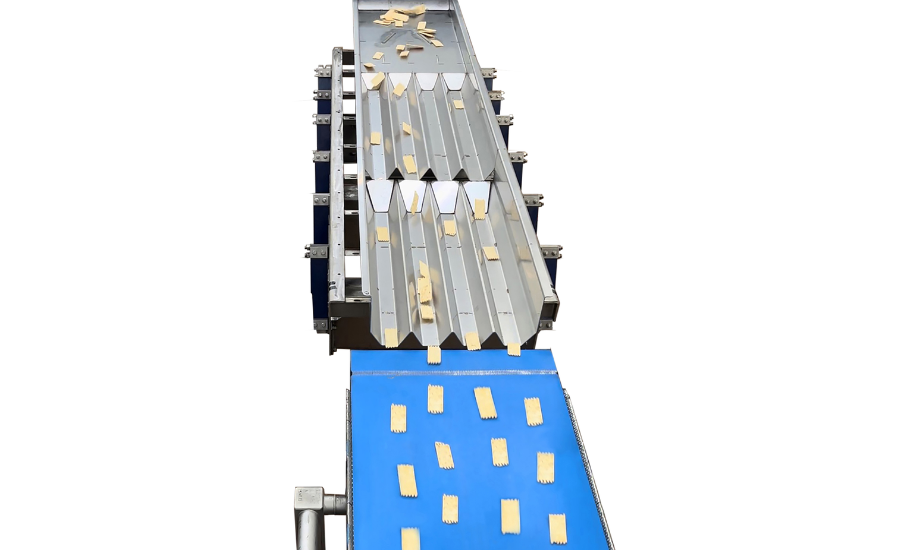
The vibratory conveying systems allow for the minimization of manual packaging. Courtesy of Key Technology
Key Technology, a member of the Duravant family of operating companies, has introduced their new vibratory conveying systems designed to feed pick-and-place robots on packaging lines. Each series of integrated conveyors meters, separates, singulates and/or aligns product, depending on the application, to provide the optimal product separation, speed and orientation for ideal presentation to the robotic system for pick-up. By minimizing hand packing, these new systems help increase production efficiency, reduce labor and improve sanitation.
“As a food processor grows, they come to a point when hand packing has to be minimized or is no longer feasible. Manually packaging, especially 24/7 with several workers at a time, is expensive, inconsistent and can be unsanitary, plus these jobs are physically grueling with high turnover. It’s a huge pain point for many of our customers – automation makes sense,” said Jack Lee, Duravant Group President - Food Sorting and Handling Solutions. “The challenge is that lining up products for presentation to a pick-and-place robot requires a degree of precision that’s unusual in conveying. Drawing on our team’s deep expertise, we work closely with each processor to design the perfect solution for their specific application.”
Rotzinger Group Unveils a Robot with an Integrated Buffer and Hygienic Conveyor at PACK EXPO Las Vegas

The integrated solution combines delta robots, buffers and conveyors in one cell. Courtesy of Rotzinger Group
Rotzinger Group, a leading provider of automation solutions, is launching its highly advanced Robot with an Integrated Buffer and its Hygienic Conveyor for dry cleaning. The groundbreaking technologies will be showcased at PACK EXPO Las Vegas, at booth SU-7113 from September 11-13. Leveraging decades of expertise in pick and place delta robots, buffering, and conveying, the new integrated solution from Rotzinger combines flexibility, compactness, and ease of operation to boost uptime and reduce the total cost of ownership. Designed for confectionery and bakery products, the hygienic conveyor is optimized for dry cleaning, ensuring compliance with stringent food safety regulations in US manufacturing.
"We are excited to have the opportunity to connect with our North American customers and prospects in the food sector for the first time since the opening of our US site last year," said Nicolas Garcia, Vice President & General Manager, Rotzinger Group, North America. "Our Robot with an Integrated Buffer and Hygienic Conveyor have been specifically designed to tackle the escalating concerns regarding labor shortages, space limitations and heightened sanitary requirements in food production. With intuitive controls and a streamlined design, these solutions enhance productivity and optimize operations."
Cablevey Develops “Smart Cart” to Make CIP Practices Easier for Tubular Drag Conveyors

The “smart cart” allows for the cleaning of tubular drag conveyors to become almost entirely automated. Courtesy of Cablevey
To promote food safety and sanitary compliance, food packagers are increasingly seeking the ability to Clean-in-Place (CIP), an automated method of cleaning the interior surfaces of tubular drag conveyors without disassembly. Now, with the advent of mobile tools like an innovative “smart cart” that quick-connects to any tubular conveyor and enables simple, customizable “single button cleaning recipes,” CIP is becoming easier, faster, less labor-intensive, more repeatable, and almost fully automated.
Tubular drag conveyor systems gently move product through a sealed, enclosed tube using a drag cable and circular discs pulled through on a loop, so they are ideal for delicate items. In a wet CIP process, the system is flooded with water, flushed, rinsed, cleansed, and thoroughly sanitized. The process thoroughly flushes out any potential allergens like nuts or gluten from conveying equipment and can be used with a variety of food types such as nuts, grains, cereals, powdered soups, and frozen fruits and vegetables.
Dorner and Garvey Showcase the AquaGard GT Conveyor at PACK EXPO Las Vegas

The AquaGard GT marks the inaugural joint venture between Dorner and Garvey. Courtesy of Dorner
Dorner and Garvey, both Columbus McKinnon brands, recently showcased the AquaGard GT Conveyor at PACK EXPO Las Vegas. Their inaugural joint venture, the AquaGard GT is a conveyor system that has been meticulously designed and crafted to address the needs of accumulation-type applications, thereby preventing bottlenecks in various industries such as packaging, bottling, dry food processing, and part handling. The AquaGard GT plays a crucial role in maintaining smooth and efficient workflow in these industries.
Key Features
- Materials and Hygiene: The AquaGard GT is constructed using premium materials. All components, except for the motors, are crafted from either stainless steel or FDA-approved plastics. This choice of materials is particularly suitable for environments that require regular wipe-downs or occasional washdowns of the conveyor. This ensures both longevity and hygiene compliance.
Looking for a reprint of this article?
From high-res PDFs to custom plaques, order your copy today!