Industry Q&A: Static Control
Static Prevails: A Look at the Generation, Management of Static

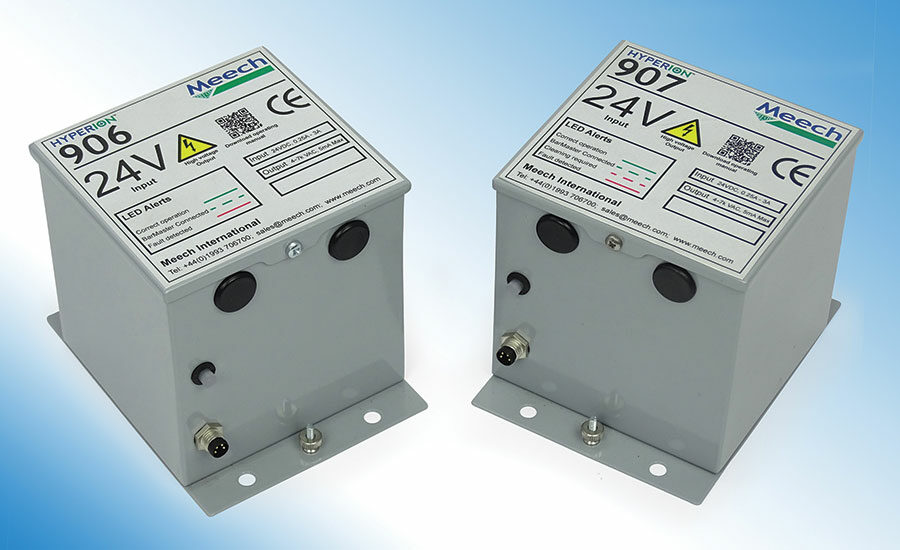


Matt Fyffe, VP/general manager, Meech USA, talks innovation in static control equipment, the science of static and why it needs to be taken seriously in converting environments.
Q: What’s new in the world of static control/static control equipment?
A: We have recently expanded Meech’s Hyperion range of static control systems with the introduction of the 924IPS, a bar powered by 24V, with an internal power supply (IPS). This makes it easier to install, as there is no need for an external power supply or running of high voltage cables around the machine.
The 924IPS is a compact, short-range pulsed DC ionizing bar that can be applied in a variety of sectors, such as converting, labeling and flexible packaging. At 32mm high, the 924IPS is the most compact pulsed DC bar available on the market, which makes it suitable for installation in challenging positions that would normally require an AC bar. The system employs the same 4-pin M8 connector and shockless titanium emitter pins as other Hyperion bars, while also having an IP rating of 66, making the bar suitable for use in harsh environments. It’s the first of our bars to feature adjustable output voltage, which is useful in particularly sensitive applications, such as RFID, and gives complete control over the output. Similar to other Meech Hyperion bars, we have incorporated a “clean pins” alert into the design of the 924IPS. This is a vital feature, where an LED will illuminate either green or flashing red depending on the cleanliness of the bar. This, in turn, helps the user determine whether good ionization performance is being achieved.
Q: Fill in the blank: If I’m a flexible film converter/printer and I’m not taking static control seriously, _______ has the potential to happen. Why?
A: Contamination. If a static charge is generated as the coated paper or film is unwound from a roll, it is single-handedly capable of attracting airborne dust to the web from several feet away. Once the dust is on the material, it can cause defects in print quality.
Furthermore, a high static charge can also cause problems with ink adhesion, as it is likely to repel the ink from the material surface and affect the overall quality of the finished product. Not only does this scenario lead to increased production costs, it can also lead to reduced production speeds.
Q: Static control is important in terms of contamination control and minimizing equipment issues, but it’s also key to operator safety. Can you explain how static could be harmful to unsuspecting personnel?
A: An electrostatic discharge can not only give shocks to operators, it can also result in considerable damage within a production environment. For instance, when static is present on a web, even in small amounts, it can still cause issues during the winding process. As the material is wound up, the so-called “battery effect” can result in a huge charge being accumulated. A charge like this will obviously be responsible for attracting high levels of contamination to the web’s surface, but it can also produce a discharge that could result in physical injury, or potentially cause fires or severe damage to in house equipment.
Q: What are the key factors that influence the generation and maintenance of static? How does today’s equipment help manage these factors?
A: Static is a common phenomenon that affects a number of industries as well as flexible packaging, and as machinery speeds have increased and an expanding number of synthetic materials have been developed, the negative effects of static have become more apparent. Many factors affect the generation and maintenance of static. Among these we find humidity and changes in temperature, but it is also worth considering the type of material involved in a production environment. Plastic films, in particular, generally maintain static charges for a long time due to their high resistivity. Whenever the raw structure of a plastic material is changed, the process will manifest an electrostatic charge, which invariably leads to static problems on the production floor.
As health and safety legislation has tightened, and consumer expectations and the increasing need for efficiency and cost-savings on the production floor have grown, a need has emerged to resolve these static problems. And to meet this demand, innovative solutions such as anti-static bars and ionizing air curtains have been developed, often tailored to meet the specific requirements of the customer.
Looking for a reprint of this article?
From high-res PDFs to custom plaques, order your copy today!