Flair Plays Matchmaker with Color Management System
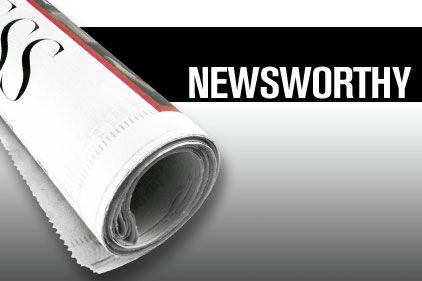
Flair Flexible Packaging has instituted its highly detailed, rotogravure-specific color management system, designed to match customers’ colors and deliver consistency.
This system encompasses the entire print process, as Flair is involved with everything from artwork creation through the final printed product. Spot colors and process image colors are carefully analyzed and customized where necessary to ensure proper reproduction. Electronic verification proofs, color match proofs, CIE Lab value referencing, and multiple quality checks throughout help to control the process and deliver color consistency on each order.
Once electronic and color match proofs have been approved, Flair works closely with the plants to ensure that cylinder engraving and printing are completed to Flair’s stringent quality standards in creating the final product. Tested and rated highly by customers, this process allows Flair to be deeply involved in matching the colors and final packaging arrangement to differentiate the product. All aspects of the printing process are certified in Color Management, including Flair, ink suppliers, presses, and cylinder engravers.
In today’s competitive packaging culture, reverse rotogravure printing is the most sought after print process for numerous reasons. The ink is trapped between two layers of film so the integrity of the image is protected from scrapes, scratches, and fading. The process not only creates striking images, but customers also have the ability to specify any and all necessary film functions (air and moisture barriers, physical resiliency, UV protection, and more) at the lowest possible cost-to-performance ratio.
Overall, Flair’s design group has a well-established and highly respected design, prepress, and production process, creating the precise color match between the customers’ vision and the final printed product.
Flair Flexible Packaging Corp.
(920) 574-3121
Looking for a reprint of this article?
From high-res PDFs to custom plaques, order your copy today!