Healthcare and pharmaceutical plastics trends highlight importance of innovative marking and coding solutions
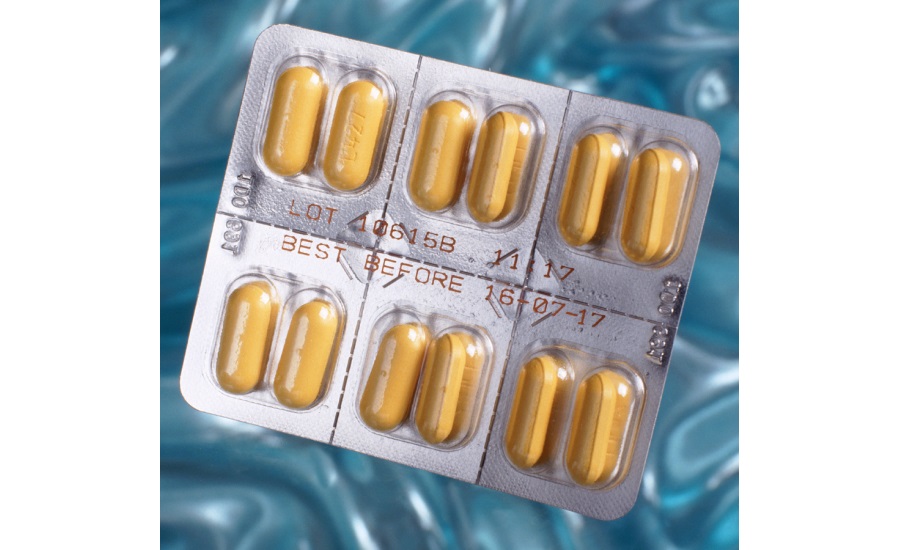
The global plastics packaging market, defined as bags, pouches, films, containers and envelopes made from plastic, is expected to reach $370.25 billion by 2020, growing at a CAGR of 5.2%, according to a recent report. Driving much of this growth is the healthcare and pharmaceutical industry, which is increasingly utilizing plastics packaging due to both its product safety benefits and consumer demand.
Videojet Technologies (videojet.com), a leader in coding, marking and printing solutions, shares how manufacturers can best prepare for addressing this growing trend while continuing to meet stringent industry regulations, maintain traceability and packaging safety, and optimize uptime.
Marking and Coding Solutions Ideal for Challenging Plastics Packaging
Plastics can offer advantages over other packaging types because of their tamper-resistance, hygienic properties, resistance to breakage and the ability to help retain the medicinal properties of the contained drugs. However, with slick plasticizers, it can be challenging to apply codes to plastics packaging with good contrast and permanence. Videojet suggests appropriate printing and marking technologies to address this concern.
• Continuous Inkjet (CIJ) printers are a versatile coding solution for plastics. Suppliers offer a growing number of application-specific fluids, including a variety of ink colors for optimal contrast as well as fluorescing UV readable inks for covert coding applications. CIJ printers integrate easily into production environments, enabling coding on the top, bottom and side of plastics packaging.
• Laser Marking Systems can create indelible marks directly on bottles, labels, blister foils and a variety of other pharmaceutical packaging. For multi-lane coding applications, a properly specified laser can mark all lanes at once. Laser marking is also valuable for its high resolution capability on certain pharmaceutical packaging, like droppers and vials, which offer small marking windows. Given the wide variety of substrates in the pharmaceutical industry, a technology partner that offers CO2, fiber and UV laser sources is best positioned to identify solutions to meet application requirements.
• Thermal Transfer Overprinting (TTO) is another suitable option for plastics packaging and labels. It is easily integrated into systems that involve filling pouches, bags, label applicators and other flexible containers. TTO offers high resolution printing of alphanumeric text, bar codes and simple one-color icons, and may be integrated into the web handling of packaging systems with bracketry specific to OEM packaging equipment.
• Thermal Inkjet (TIJ) printers have traditionally been valued for their ability to print 2D DataMatrix and other high-quality text and bar codes, but this technology was limited to coding on porous substrates. Recent innovation in TIJ technology, however, has produced solvent-based inks capable of adhering to common non-porous substrates used in healthcare and pharmaceutical manufacturing such as films, blister foils and coated labels.
Healthcare and pharmaceutical manufacturers should take a comprehensive, measured approach when evaluating marking and coding solutions for their plastics packaging applications. By understanding the unique features of each technology, manufacturers can choose the right solution for their needs and benefit from clear and permanent codes on plastics packaging, thereby helping to ensure that traceability needs are met. At the same time, the right marking and coding solution can provide manufacturers with reduced maintenance and greater uptime.
Looking for a reprint of this article?
From high-res PDFs to custom plaques, order your copy today!