Packagers flex their creative muscles
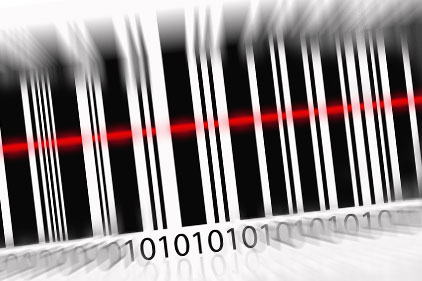
Innovations in flexible packaging fall into two primary categories: machinery advancement and new product development.

According to a recent study by The Freedonia Group, Inc. (www.freedoniagroup.com), U.S. demand for flexible packaging is projected to increase by 5.1% per year due to advantages such as aesthetic appeal, portability, reduced material use and lower shipping costs than rigid containers. In order to be on top of the dynamic and evolving industry, producers of flexible packaging must be able to adapt an out-with-the-old, in-with-the-new attitude. Two integral ways that flexible packaging manufacturers can stay ahead of the curve are using the latest and greatest machinery and endeavoring to provide the most cutting-edge products.
Before the products that utilize flexible packaging can make it to the store shelves, they have to make it out of the plant. One way companies can make this process as efficient as possible is to equip with the most effectual machinery available. Two new technologies for DP Drop Packer Systems from Combi Packaging Systems LLC (www.combi.com) can aid in this process: the Product Infeed Drying System and the Pull Nose Delivery System. The Product Infeed Drying System is intended for use with sealed plastic bags and pouches of liquid products. Without this technology, products come out of a wet bath and must be dried and shingled by hand before being hand packed into manually erected cases. This system allows for automation of this entire process. Wet plastic bags are fed to an infeed conveyor which uses air blowers to dry the product before the bags are transferred to a belt conveyor that extends and retracts, shingling the product as it drops onto a Bombay door in a pre-determined pattern. This system produces 50 bags per minute and reduces labor requirements from seven people to two.
To read this article in the digital edition, click here
Looking for a reprint of this article?
From high-res PDFs to custom plaques, order your copy today!