Web Handling
Print Industry Leaders Give Back with The Web Handling Handbook
A new handbook from three experts documents the challenges and the evolution of web handling over the last four decades in the converting and printing industry.

We caught up with the authors to discuss current servo technology trends, today’s workforce challenges and new film properties as it relates to web handling.
After a great deal of success in a long career, many leaders give back to their industry by extending their knowledge to the next generation. In the printing and converting space, there are three industry professionals doing just that: Dr. David Roisum, Timothy J. Walker and Dr. Dilwyn Jones. These three men collaborated and put together an extensive book called The Web Handling Handbook, which addresses web handling execution for a large range of applications, including calendaring, coating, laminating, printing and other web processes.
As older operators start to retire, many converting, printing and laminating companies are facing challenges in documenting internal web handling processes, and this new book aims to fill in the gaps and provide industry context. The handbook delves into fundamentals and examines the evolution of web handling, but it also touches on advanced concepts, including recent research findings and highlighting these practical applications.
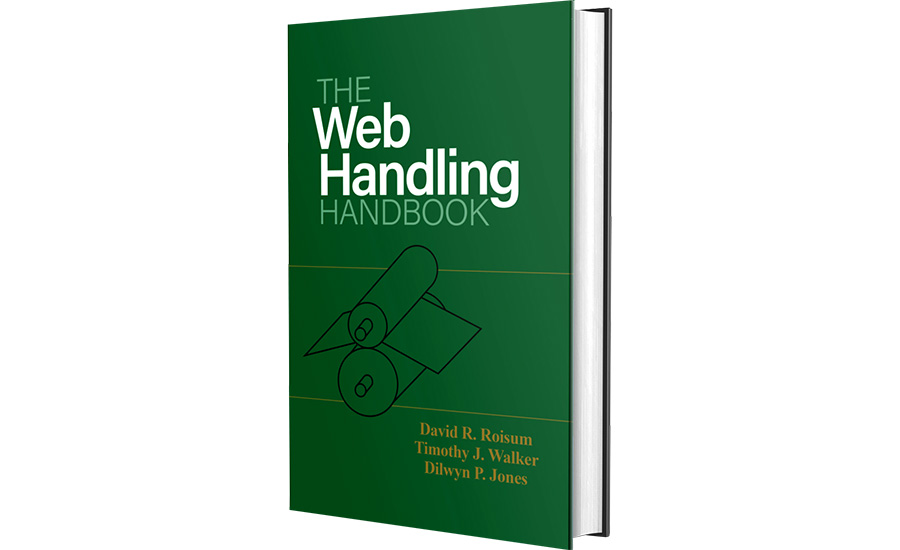
Photo courtesy of DEStech Publications, Inc.
Flexible Packaging reached out to the printing and converting experts and asked about servo technology advances, workforce issues and new film material related to web handling. The answers have been lightly edited:
Flexible Packaging: As mentioned in the book, drive and motor technology has changed the most during the book’s timeline. How did modern servo drive and motor technology move the needle for a new era of web handling? What other machine automation trends are emerging, such as capturing machine data and performance?
Dr. David R. Roisum: Servo drives revolutionized our industries by supercharging positioning systems such as digital lineshafts, MD registration and package assembly components. However, the blessings were more mixed for a time for the more mundane and more common tension and force controls. These new drives were so “hot” — responsive — that they presented yet more ways to get into control trouble until the drive engineers literally went to school on them. Now, most problems are knowledge shortcomings rather than any limitations of the hardware or software.
Dr. Dilwyn P. Jones: Servo drives bring a faster response and more accurate positioning. Coupled with machine software, they can automate the machine setup, for example moving rewind arms and knives in order to change the cut pattern on a large slitter rewinder. This can be completed in seconds, compared with maybe an hour of manual repositioning. This gives an increase in productivity and less risk of error. Similarly, flying splices and roll changes can be carried out automatically, more quickly, while maintaining product quality.
Improved connectivity and availability of data is also being used to monitor the duty of machine elements and detect any deterioration in performance due to wear. This can even report back to the machine supplier so that spares can be sent in good time.
Timothy J. Walker: The real benefit with servo technology has been in registered processes where the web has a machine direction repeating pattern from printing, rotary die-cutting or discrete part attachment, such as island placement. Servo eliminates the process variability and maintenance of gears, belts, couplings and line shafts. The greatest challenge of servo technology is the big shift from mechanical design to electronic controls. Many equipment suppliers were mechanically strong, but traditionally weaker in electronics and controls. With servo technology, suppliers need to be strong in both areas.
Flexible Packaging: What’s going to happen with web handling in the next three to five years, as it relates to the workforce — operators, suppliers and management? Are there any lessons from your book on the web handling technology advances and how it affected the workforce back then that could be applied to now?
Walker: Our goal in putting together The Web Handling Handbook was to create the book we wish we had 30 years ago. Anyone starting out or moving into processes based on web handling (e.g. roll-to-roll processes) should dig into this book at regular intervals. The principles of web handling are built into most machines today as best practices are shared and repeated.
Beside our book, there are so many more rich resources to increase your web handling expertise. Dave Roisum and I have websites with material that complements the book. Dave also has a YouTube channel with many practical topics.
For advanced engineers, ShareOK.org has free access to all the Web Handling Research Center’s graduate student theses and proceedings from 20 years of The International Conference on Web Handling. You may not become a web handling expert overnight, but you could likely get there three times faster than we did by living through it.
Jones: On modern machines, all the operating conditions are automatically set up from a recipe. This removes the need for operators to “fly” the machine, with chances to make errors. Some may regard this as de-skilling, but it's essential to improve process consistency and maintain high quality. Process consistency also relies on reducing variability in feed material and machine conditions, so there is confidence that standard conditions will work and there is no need for real-time manual adjustments. Of course, it does take time and maybe negotiation between shift teams to home in and agree standard conditions.
There are tasks that the operators do — loading cores and unloading rolls, taping on, setting positions of knives, sensors etc. It is good to involve them in assessing where the problems are coming from and suggesting changes, modifications etc., to make the task easier and less prone to degrade quality. Better data from the machine allows problem solving to use fundamental measures of tension, nip and other variables, so it is essential operators learn about this rather than flying blind.
Roisum: Machine operation is becoming ever more complicated. Even a modest rewinding machine has more control settings and readouts than a light airplane. Laminators and printing presses are more like small commercial jets. Thus, the two current paths are likely to diverge even further. The first is toward the “one button” operation where the green button is pushed at the start of the shift and the red when troubles arise and engineering is called in. There are winders that get pretty close to that now where all roll handling, threading, splicing, labeling and so on are done by a combination of winding machine, hard automation or robots. The second is the uber-skilled and trained technician/operator who can not only troubleshoot maintenance issues, but also product/process troubles.
Flexible Packaging: What are your thoughts on sustainable films and how it relates to web handling? What are the challenges that web handling machinery will have adjusting to a bigger percentage of recycled material in films? Minor? Still developing?
Walker: I am skeptical about a significant increase in “sustainable films” in the near future. Estimates of polymer film recycling in the U.S. today range from 3-9%. Some European countries claim much higher recycling rates, but these numbers may be based on collection rates rather than reuse and count recycling into flowerpots and benches with little going back into films. In 2018, the recycling world was shocked as China stopped accepting waste (a.k.a. recyclable materials) from foreign countries. Based on these trends, I don’t see sustainable films greatly impacting web handling for many years.
Roisum: Web handling is agnostic to materials. We serve thick and thin, narrow and wide, and sustainable and unsustainable alike. What we do offer is waste reduction. Easily a few percent of waste, delay and customer complaints are web handling related. This amounts to billions of dollars per year worldwide that we can help with. This will only increase unless web handling is deployed because the trend to ever thinner materials and ever-faster speeds is also ever more challenging to run without wrinkles, web breaks/jams, winding troubles and more.
Jones: Much depends on the quality and consistency of the reclaim feed. It should not contain particulate contamination, which can initiate breaks and tears. Also, properties such as surface roughness, coefficient of friction, Young’s modulus and yield or break strength should stay within defined bounds. But even with these change it is usually possible to change tensions, nips, etc. to maintain quality and productivity. Recycled material probably has more influence on the end product, for example color, haze, adhesion and tear strength.
Looking for a reprint of this article?
From high-res PDFs to custom plaques, order your copy today!