In late March, the Recycling Partnership in Falls Church, Va., announced a second round of grant funding through its Polypropylene Recycling Coalition, which will distribute around $1 million in catalytic grants to advance polypropylene recycling in the U.S. This second round of investment for the coalition targets sortation of polypropylene (PP) at mechanical recycling facilities (MRFs) and local consumer education efforts.
Specifically, the funding will be directed to three MRFs across the U.S., making a total of seven MRFs since the inception of the PP coalition. The funds will improve curbside PP recycling for an additional 3% of all U.S. households and increase the recovery of 4.3 tons of PP annually.
“We continue to encourage all companies that use polypropylene to join us in being part of the solution to ensure greater and better capture of this recyclable material,” says Sarah Dearma, VP of circular ventures, The Recycling Partnership.
Other companies included in the Polypropylene Recycling are The Kroger Co., EFF Plastics, American Chemistry Council, Campbell Soup Company, KW Plastics, LyondellBasell and Procter Gamble (P&G), to name a few.
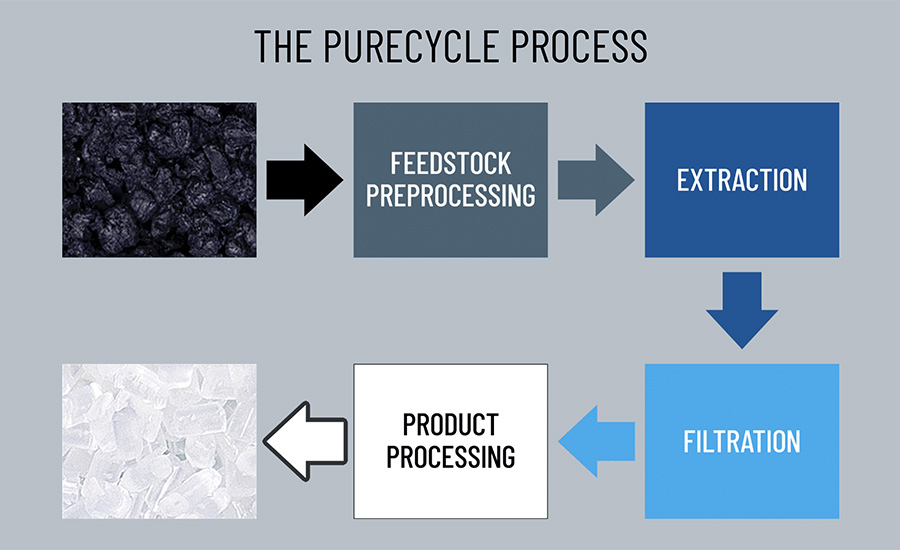
Photo courtesy of PureCycle
Dedicated To Polypropylene Recycling
One company very interested in recycled PP is the above-mentioned P&G, and the company has been spending capital on researching this popular material within the company for the last 15 years.
Why? PP is the company’s lead plastic material and, if displaced, could aid in the company’s goal of reducing 50% of its virgin plastic from its products by 2030. In the early 2000s, P&G searched for a third-party company to recycle PP since the Cincinnati-based CPG uses the plastic in more than half of all its products.
“We use PP in a variety of applications, whether it’s non-wovens, films, injection molded parts like toothbrush handles, razor blade handles, anti-perspirant canisters or all sorts of packaging components,” says Dr. John Layman, R&D director of sustainable materials at Procter & Gamble in a recent virtual Q&A session.
Since P&G couldn’t find a company recycling PP, P&G’s 8,000-strong technologists began research and development on the issue. The P&G lab came up with “a purification process — an IP recycling technology — that creates a solvent from recycled PP,” according to Layman. The solvent would be the base material to create PP for packaging.
After P&G demonstrated the technology in a lab, it turned to Innventure, a venture capital company that specializes in developing proprietary IP technology, which helped P&G hand off the technology to PureCycle, a recycling company that’s accelerating the commercialization of a polypropylene recycling technology, which would be tasked to commercialize the technology on a large scale.
How much PP could be produced? Once fully matured and commercialized, PureCycle hopes to produce more than 1 billion lbs per year. "PureCycle's proprietary recycling technology was developed by P&G, and it's this type of top-down investment that's driving the circular economy," says Tamsin Ettefagh, chief sustainability officer at PureCycle CSO.
During the virtual Q&A session in late 2020, hosted by PureCycle, Layman provided a technology update, insights on the current process and how the company will scale this technology. “P&G works closely with the PureCycle team in Ironton, Ohio, where the first Feedstock Evaluation Unit (FEU) is located, as well as the first commercial plant will be,” says Layman. PureCycle’s early goals are to reach 107 million lbs of recycled PP content and then to scale to 165 million lbs per year.
“The unique recycling process revolves around removing solid waste from PP waste batches,” says Layman. With this in mind, PureCycle takes solids that are removed from the PP — pigments, pieces of wood and metal — and activates a pressurized process that produces atmospheres.
The current state includes a pilot plant that has led to a continuous process manufacturing method that allows for larger amounts of PP to be recycled.
“What’s great about the FEU process is we’re able to produce continuously,” says Layman. “Instead of doing a pound a day with a batch process, we can do several pounds an hour — five to 10 lbs per hour continuously — which affords us the ability to make more material and do testing at scale.”
While the technology has its own unique IP patents, the continuous processing technology includes well-known distillation principles for regular resin production such as extraction columns, extruders and candle filters.
And there’s been many lessons learned, one being precipitation that’s caused clogging. “We’re making sure the temperature and pressure are maintained, which enables us to keep the thermodynamic properties of the process in line,” says Layman. “From there, we can ensure there’s no precipitation, unwanted precipitation of the polymer that would cause clogging and disrupt production.”
Layman describes the final solvent purification as certainly not brand-new, but the final product, a particular alkaline solvent, needs precise temperature and pressure processing.
PureCycle recently received more than $700 million from a public offering and accelerated construction at the Ironton, Ohio location. The money will build three more plants, comprising 185,000 square feet on 23 acres. While the company hasn’t disclosed a final date for production, PureCycle is keeping its focus on the 170 billion lbs of PP used last year, with only 1% being recycled. Stay tuned.