Mondi Invests in Liner Films Business
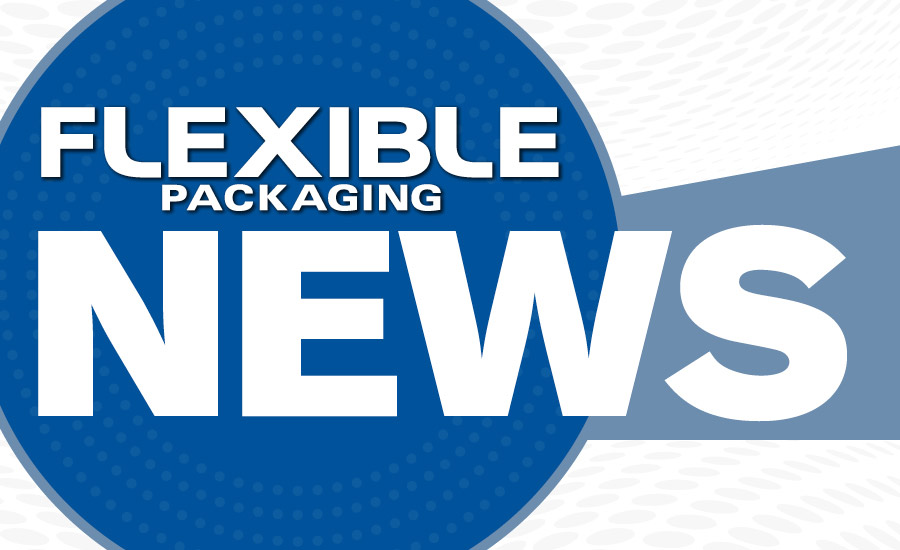
Mondi is investing in its Styria, Austria, plant to further boost its ability to offer safe, clean, environmentally friendly liners for Flexible Intermediate Bulk Containers.
“Mondi’s FIBC liners ensure clean food processing and are ideal for milk powder, other foods, pharmaceuticals and additional applications,” notes Stefan Pfundner, business solution manager, Mondi Technical Films.
“Not only do Mondi’s FIBC liners advance customers’ processes and logistics, but their superior quality reduces the amount of raw materials used and offers an environmentally friendly alternative to traditional liners.”
The Mondi Styria film extruding plant already is well known for its outstanding hygiene standards and innovative sustainable product development. The site has extensive experience in developing more environmentally friendly products, including thinner, downgauged films and ply constructions ready for recycling. Now, with its latest innovation, Styria is enabling the elimination of aluminum inner layers in FIBC liner films.
Mondi is installing new equipment at Styria to make high-barrier, side-gusseted tubes for FIBCs. This latest equipment upgrade will make Mondi Styria the only plant of its kind able to produce these types of tubes in such food-clean conditions. That facility has earned three straight “AA” certifications per the British Retail Consortium (BRC) global standard for packaging and packaging materials. That certification gives qualifying brands an internationally recognized mark of quality, safety and responsibility.
The new side-gusseting device will enable Mondi to provide converters with tubes up 4,400 mm in total circumference. It will come equipped with a special HEPA air filter to clean the air within the blown-film bubble to remove bacteria and particulates, yielding nearly sterile conditions.
“Ensuring appropriate levels of hygiene during production and packaging is vital for suppliers of foods and other products,” Pfundner said. “Due to our well-established relationships with some of the leading multinational brands, as well as with the leading producers of such demanding products, we decided to extend our bulk-packaging portfolio by adding production in Styria of high-barrier, side-gusseted tubes.”
Liners produced from high-barrier, side-gusseted tubes minimize the risk of contamination on the inside, compared with liners produced from flat film or foil, such as aluminum liners. Mondi also can adapt the barrier properties according to the needs of the product, to protect against odors, moisture and the like. With such tubes offering a viable alternative to aluminum liners and other kinds of laminate structures, FIBC packagers potentially can not only save money, but also reduce their carbon footprint.
Mondi additionally can tailor-make multilayer films using a variety of structures, from PE to PE/PA and PE/EVOH to 7-layer PE/PA/EVOH structures, additives and colors to provide solutions for all kinds of industries, from food to chemicals, minerals or pharma.
The properties of Mondi’s FIBC liner films make them ideal for food, pharmaceutical and other critical applications, while also helping to advance bag manufacturers’ processes and logistics. These films boast stringent certifications that document their excellent performance related to oxygen and moisture barriers, anti-static properties and overall mechanical strength.
Mondi
Looking for a reprint of this article?
From high-res PDFs to custom plaques, order your copy today!