Industry Q&A: Coating/Laminating
Collaboration, Cooperation Spur New Developments in Coating and Laminating

We caught up with Giancarlo Caimmi, commercial director, Nordmeccanica Group, for a conversation on the latest innovations in the coating/laminating space.
Nordmeccanica and Henkel debuted a new barrier coating last June in Munich. Can you explain the significance of this innovation?
Caimmi: Nordmeccanica and Henkel partnered for a R&D cooperation, BarrierEnhanceTech Alliance. It is our opinion that barrier is one of the hot topics in packaging, and the ability to provide converters with innovative solutions will allow for unprecedented developments. Two market leaders in the relevant field therefore decided to open a new project of research targeting barrier. At Nordmeccanica, we saw an opportunity that would develop significant synergies for the two divisions of our company: coating and laminating, and vacuum. In both areas, our contribution would have been extensive know-how and the access to hardware to speed development as needed. Henkel involved its best resources in terms of people and laboratories (not to mention the knowledge from one of the largest chemical companies in the industry). It was a perfect match. It all evolved as a cooperation of this nature may allow for: The first product from our alliance is now commercial.
The first target of the research cooperation with Henkel is a top coating. It’s easy to apply, able to significantly enhance the barrier and, perhaps most important, reliable in barrier efficiency.
The innovative formulation features two impressive results. The first is an unprecedented efficiency in the protection of a vacuum-coated AlOx layer. Converters are familiar with aluminum oxide. It is a transparent metallization that features very high barrier properties while allowing to see through the laminated compound. Those good properties have been counter balanced to date by a high degree of fragility shown by the AlOx layer. The fragility results in a significant decay of the barrier values as the AlOx coated compound goes through the normal steps of a conversion process: printing, lamination, slitting, bag making. This makes AlOx a technology that’s interesting to brand owners but feared by converters. Now, thanks to the innovation presented by Henkel and Nordmeccanica, the barrier properties of the coated AlOx compound remains unchanged going through printing, lamination and slitting. There are no negative effects triggered by these processes to the barrier values.
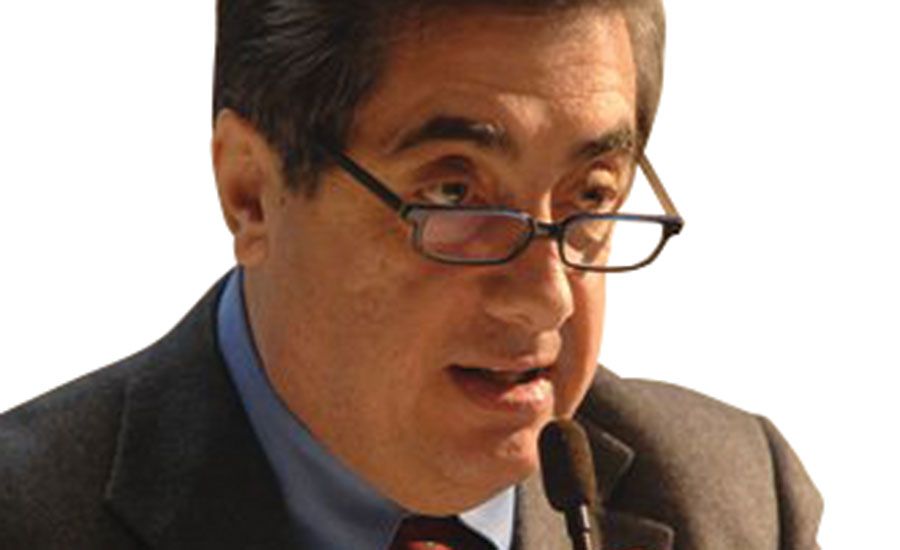
The second impressive result is the dramatic increase in barrier properties of a regular metallized film once the new coating is used as primer before the metallization process. Slide 2 offers the barrier values of the final compound once the base film is PET.
Converters can now enjoy the advantages of AlOx and the ability to make a transparent metallization easy and safe to use. They can now look into very high barrier metallized compounds as a serious alternative to foil. These are two significant results in critical area.
Similarly, can you speak about the significance of the laser die cutter integration into solventless lamination? Do you foresee a future where more and more components are integrated into coating/laminating machines?
Caimmi: Coating and lamination will remain a territory of growth and innovation for years to come. It is the nature of our industry and it is the effect of the latest development in e-commerce packaging, requiring increased strength and innovative properties. It is natural for the company that has developed the most significant innovations in the industry to stay focused on what is new. We know Nordmeccanica is a leader because we believe in this industry and we constantly invest in the future. In the case of laser die cutting, we have witnessed a trend growing in Europe. A few local converters started experimenting with laser die cutting. We delivered a few machines ready for laser and a few with a laser factory installed. They offer great advantages compared to a mechanical die. Laser allows for operation on board the laminator during lamination, and it enables converting at high speeds. Finally, laser permits cutting at whatever shape at the cost of a digital file.
A see-through window cut in a pouch is intended to show the product while featuring an outer layer of paper and a protective inner layer of film. That was the trigger. More and more brand owners, especially in the organic segment, have transitioned to paper as the outer layer. This is especially true in Europe. Laser has alternative applications that are very popular, such as micro-perforation, macro-perforation, re-closable lids, easy tear, etc. These are all application easily implemented with a laser installed on board the laminator. In cooperation with SEI Laser, a market leader in the laser industry, we have introduced a significant innovation by growing the laser and the laminator to a high degree of integration. We took care not only of fundamental aspects such as quality, productivity and reliability, but we developed the integration with the utmost attention to safety, in full compliance with the most stringent international body of rules.
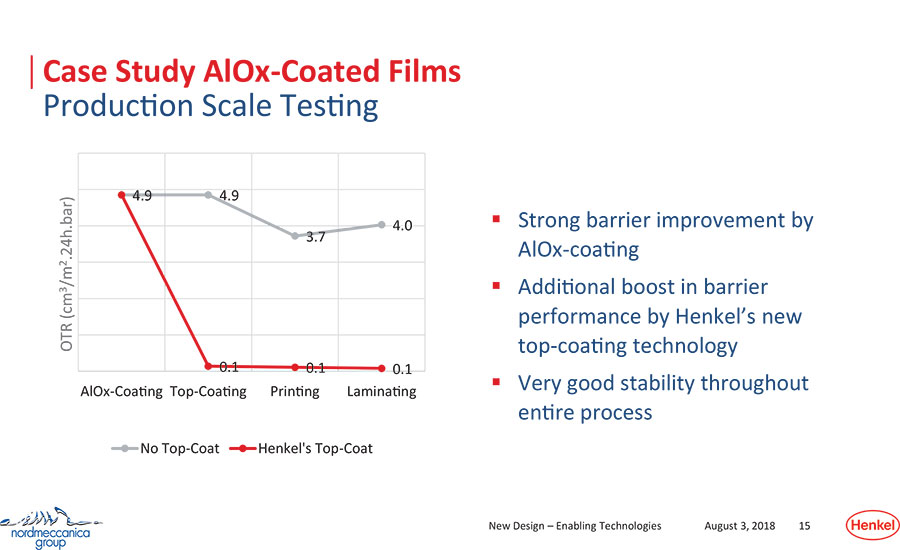
Aside from what we discussed earlier, is there anything else new in coating/laminating or with Nordmeccanica?
Caimmi: On average, we introduce two significant innovations per year. Most of them are defined by industry experts as “industry-changing innovations.” These aren’t just product developments, but significant creative innovations. That is one of the things we do best and we will continue in that direction. We do not discuss projects as they are under development. Some of them may generate no results while others will make rumor. It is the nature of innovation: having the strength, know-how and determination that allows for venturing into unexplored territories. I can promise you that for years to come, we will disclose innovations that will play a role in the growth and continued success of our industry.
It’s been about three years since Nordmeccanica hosted the grand opening of its North American HQ on Long Island. Can you reflect on the headquarters and explain how having this presence in the U.S. has helped the company?
Caimmi: Nordmeccanica products have been distributed in North America since the mid-90s. We opened our first subsidiary in Long Island, New York, in 2002. In 2015, we moved in our fully owned location. Since the grand opening, the square footage of inventory at our location has doubled, and the team of sales and aftersales professionals has more than doubled. That is definitely a consequence of our growth and a reflection of the level of appreciation of customers have for our products and services. We are particularly proud of our leading market share in North America - a market share that exceeds our average in the rest of the world. North America remains the most challenging market to serve, as expectations are at the highest levels.
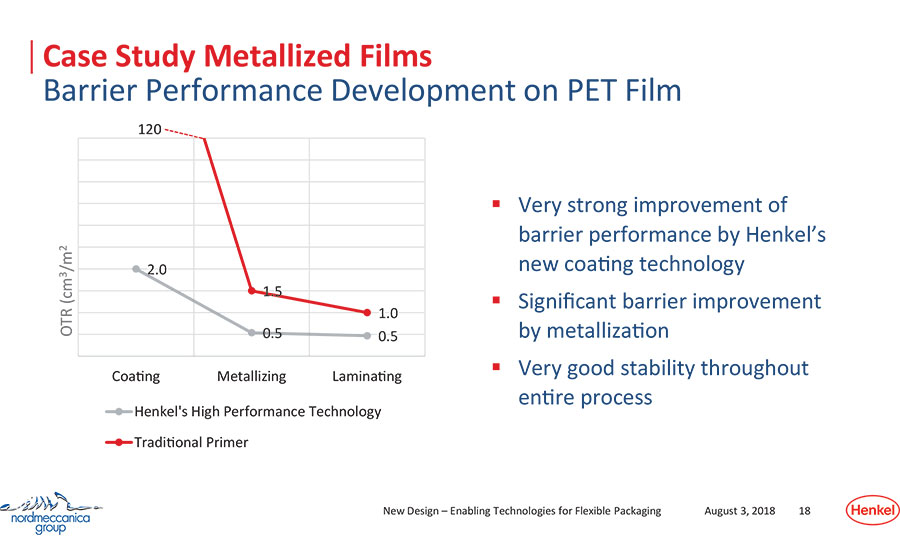
We know we can provide the best technology in the industry, but we would have never been so successful in a critical market without the understanding that services here are as important as the product is. It is intuitive that to serve efficiently, a market requires a direct presence. Therefore, the role played by our subsidiary is perfectly reflected in the diagram of sales during the past 25 years in North America. The diagram shows how significantly our Northern American branch impacted our business. Positive results call for more positive results, and it is definitely the Nordmeccanica policy to keep improving as the number of our installations keeps growing. We are in fact honored and thankful for the preference granted our way, and to say “thanks” is to keep improving our products and services.
Is there anything else you’d like to share about coating/laminating?
Caimmi: Coating and lamination remains the “money shot” in the flexible packaging industry. As the use of packaging becomes more challenging for environmental impact, energy savings, improved shelf life, and more demanding mechanical and chemical resistance grows, so grows the importance of conversion and profit margins. It is about more efficient lamination technologies; it is about performance coatings. Investing in flexible and reliable hardware is a safe decision for years to come. As we come up with innovative solutions, we witness with our own eyes how customers become more and more profitable and successful. We love to be part of it, and we love to have had a small role in so many success stories.
Looking for a reprint of this article?
From high-res PDFs to custom plaques, order your copy today!