Technology: Lidding
Developments and Trends in Lidding Film for Food Applications

It’s no surprise that in the year since we looked at lidding film for food applications for Flexible Packaging’s readers, the industry has changed. We’re now seeing developments and trends in sustainability/recycling, peel and reseal functionality, and improved barrier for longer shelf life. There was also an unexpected development earlier this year: the U.S. government decided to impose tariffs on aluminum imports. We’ll begin this year’s overview there.
For decades, metallized (MET) films, especially MET OPP, have been preferred as a replacement for foil in flexible packaging applications. As the technology evolved, MET PET became an excellent choice for replacing foil in lidding applications. Today, as food manufacturers consider their lidding design, they are looking to MET PET more than ever to counter the increasing cost and limited availability of foil. Film is readily available, and the thickness of the vacuum-deposited metal is only a few hundred Angstroms, so the impact on the price of the film will be negligible compared with what is forecast for aluminum foil.
Heat resistance is very important in lidding applications because sealing temperatures can be more than 400°F for up to a one second dwell. Material stiffness is also important, especially in “pick and place” lidding applications, where the lids are dispensed one after another. MET PET has excellent stiffness and heat resistance. While the rigors of the converting process can create cracks and pinholes in foil and compromise barrier, MET PET is extremely durable, resists cracking and pinholes, and delivers excellent oxygen barrier. In addition, with a lower density than aluminum foil, MET PET delivers more surface area per pound, so it is a smart, sustainable choice, while maintaining strong package-processing characteristics.
Dairy-food CPG companies, especially those offering yogurt, sour cream and cream cheese, are now very interested in MET PET for their lidding needs. Interest in MET PET lidding for nuts, condiments (ketchup/mustard/salad dressings), meats, cheeses and liquids is also on the rise. Peel and reseal lidding film has also become of greater interest to CPG companies, especially in deli meat and sliced cheese applications, because of the convenience it provides to consumers.
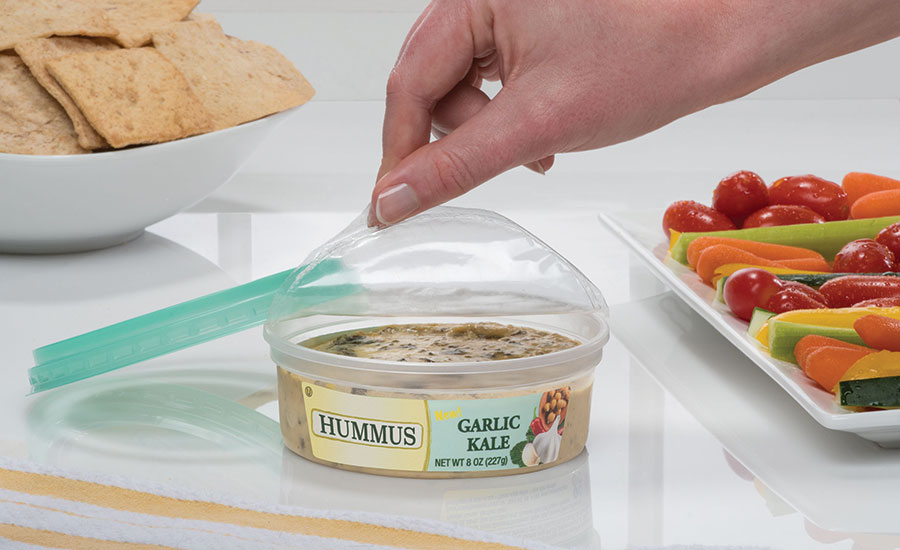
Another interesting development we’re seeing in the U.S. and Canada is with produce applications. That market has begun replacing the top of a clam shell with lidding film as a means of reducing cost and the amount of plastic used. The format is commonplace in Europe.
Companies also want improved clear, high-barrier lidding films for longer shelf life. Clear high-barrier films have been a growing trend in flexible pouch and pillow packaging because consumers like to see the product before purchasing it. The same is true for lidded packaging. The popular applications for clear, high-barrier lidding are fresh meats, deli meats, ready-to-eat meals and cheese. Most of these lidding films achieve their barrier with an EVOH sealant web or an ALOX PET film. Additionally, a new coating has been developed to deliver an industry-leading oxygen barrier that exceeds both EVOH and ALOX.
On the sustainability front, many end users announced that they are working to reduce their carbon footprint as much as possible over the next five to 10 years. Biodegradable, compostable and bio-based lidding films can help them. Toray’s LumiLid bio-based options have performance attributes similar to those of traditional lidding films for a small premium.
Some in the industry contend that recyclability is the best option in the near-term for a lidded package, and we are hearing more discussion about that solution. In June, the first U.S. pilot program for single-stream curbside recycling of flexible plastics packaging was launched by the Materials Recovery for the Future (MRFF) research program in partnership with J.P. Mascaro & Sons at its TotalRecycle MRF in Berks County, Pennsylvania. The pilot is intended to demonstrate the technical and economic feasibility of recycling household flexible packaging, which would include lidding film, from municipal residential single-stream recycling programs. We think the effort could advance the recycling of lidded plastic packaging.
What hasn’t changed in the past year is the fact that choosing a lidding film remains a very complex process. CPG companies and converters should feel confident that their film supplier has a thorough understanding of the myriad elements to be considered when they’re choosing a lidding film.
Toray Plastics (America)
Looking for a reprint of this article?
From high-res PDFs to custom plaques, order your copy today!