Roundtable: Special Advertising Section
July 2018 Roundtable on Coating/Laminating

Giancarlo Caimmi
Commercial Director
Nordmeccanica Group
24 years with the company
(631) 242-9898
www.nordmeccanica.com
Ricky Keller
Vice President – Cast Film and Coatings
Davis-Standard
37 years with the company
(860) 599-1010
www.davis-standard.com
What’s new with your company or with coating/laminating in general?
Caimmi: After presenting the Duplex SL One Shot as the next thing in solventless lamination to the industry – a technology that won the AIMCAL Innovation award and the German Institute for Packaging innovation award last year – we are introducing two new technologies in 2018. We are talking about two innovations in the coating/laminating industry that, in full compliance with our DNA, are industry-changing evolutions.
The first is an announcement that was made on June 5 at the R2R AIMCAL Conference in Munich, Germany. It’s a new barrier coating developed in cooperation with Henkel within the activities of a new industry alliance targeted to innovations in the high-barrier segment. The innovation consists of a dry bond coating used either as a primer for regular metallization or as a protective layer for AlOx metallization. In the first application, the coating is applied to a web prior to metallization. In the second case, it is applied over the AlOx layer. The barrier enhancement properties are impressive and will bring the final barrier effect into values that traditionally are in the exclusive territories of foil. Specifically in the AlOx application, the final result is in order to shield and protect the fragile layer so that finishing conversions such as print, lamination and slitting, won’t affect barrier values.
The second innovation was introduced in cooperation with SEI laser. It’s the first ever OEM integration of a laser die cutter and a solventless laminator. Die cutting a web is traditionally performed with a mechanical die cutter. This new evolution allows users to cut a see-through window in the adhesive-coated layer. The cut is performed directly on the laminator, after the coating head and just before the lamination nip. Technology allows users to coat the adhesive right to the edge of the window. Shapes of the cut are digitally programmed and allow for incredible versatility. Thanks to proper equipment design and product integration, the result enables the two systems to work safely, reliably and consistently together.
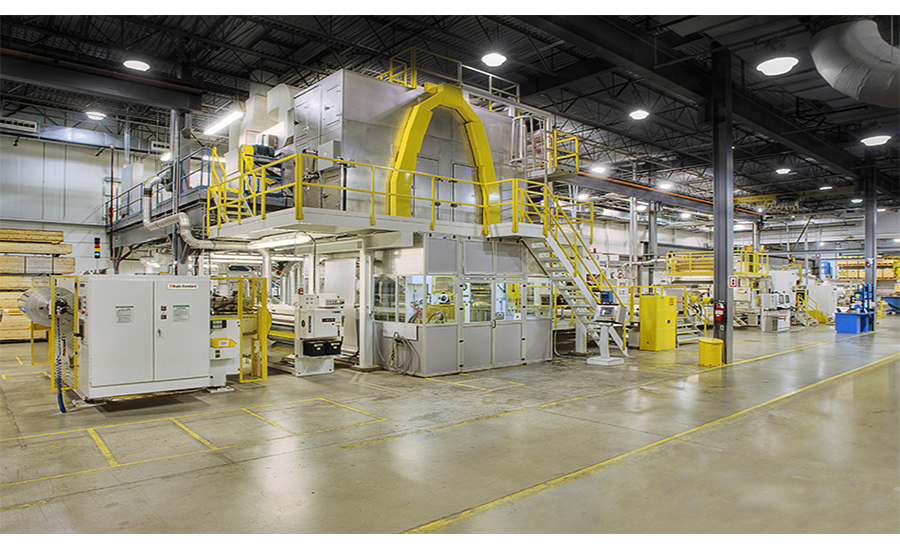
Keller: Davis-Standard supplies process machinery for film, extrusion coating and liquid coating applications within the flexible and rigid packaging, industrial and construction markets. Our philosophy is to jointly develop products, process technology and machine capabilities with our customers. To that end, we use our pilot line facilities, decades of technical development, and deep pool of engineering expertise to support process efficiency and profitability. We know end-product material costs for our customers encompass over 90 percent of their product cost, so reducing waste is our primary focus. We employ many tools to achieve increased productivity and waste elimination. Our newest coating lines for packaging regularly achieve 800 MPM. Our unwinds with high-precision splices reduce tail waste to a few inches of product. Our stationary knife winders provide a clean-cut with no fold-over for an excellent roll start, essential for high-quality roll configurations.
It seems that one of the trends in equipment today is the development of more compact machinery. Is this trend present in the coating/laminating market? Why or why not?
Keller: The required floor space of a production line is certainly an important factor, but the real driver in the converter’s cost is the amount of process waste and productivity. Reducing the space required for a machine is definitely a trend, but also needs to be balanced against safe machine operation. In some cases, compact machines do not permit good operator sight lines for best operation and function. Compact designs must take these factors into consideration.
Caimmi: It is, in my opinion, more than a trend – it is an industry requirement. The days of the “big machines” have long gone, both for “stop-and-go” setup, as well as for fully automatic equipment. We in Nordmeccanica can definitely claim this. Nordmeccanica invented the concept of compact machinery for coating and lamination application in the early ’90s. The product family was named “Simplex” and since the age has sold in the thousands, effectively changing the way to approach conversion. The compact design was not intended as an inexpensive piece of equipment, but as a very efficient machine designed for short and medium runs. Such a concept of short runs at the age was unknown in coating and lamination. Today, even the most conservative machinery manufacturers have been forced to understand that short and medium runs are not an inferior business, but just one of the shapes that the converting business can take. And, as a matter of fact, there have been quite a few attempts of imitation of our Simplex family of products. We at Nordmeccanica pioneered the concept of compact to extend to fully automatic machinery for long runs. Compact means shorter web paths, lower scrap rate, more efficient web handling, operator friendliness, lower energy consumption and more. It takes wide open eyes and a close partnership with customers to conceive industry requirements. Possibly that is what we at Nordmeccanica do best: listen to customers.
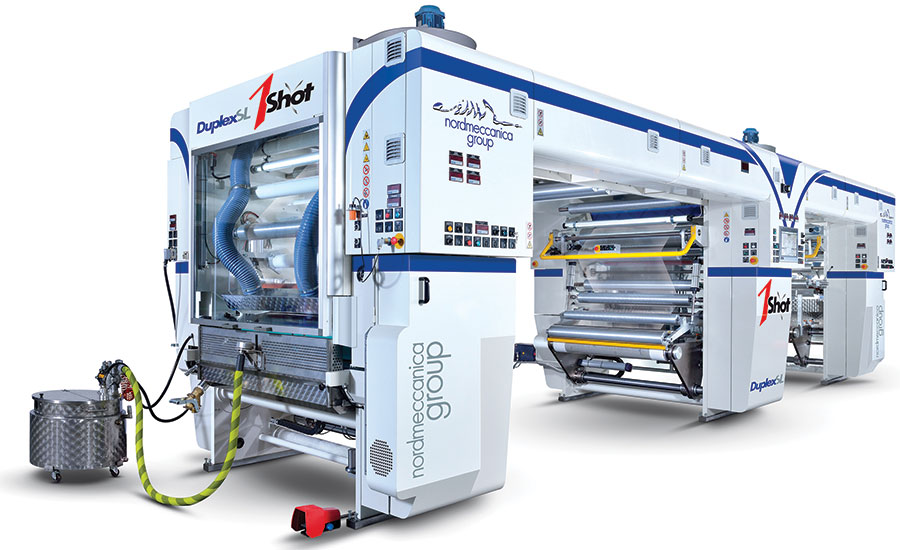
What role does coating/laminating equipment play in the trending Industry 4.0 movement?
Caimmi: Both coating and laminating are inherently recipe-driven technologies. Compared to print, which is defined as an art, both coating and lamination are way closer to the scientific approach. That is the reason why in the early days both technologies have been the territory of few large companies highly specialized in those fields. The way that the industry evolved and again, as mentioned in my previous reply, a lot thanks to the way Nordmeccanica reshaped the machine design, these days coating and lamination are at hand for every converter, no matter the size and the investment power. In the converting industry, coating and laminating are, consequently, the technologies suitable to an effective integration within the Industry 4.0 guidelines. We at Nordmeccanica are deeply involved with industry partners to integrate both machine setup at the design level as well as machine set up at the installation site within the requirements of the smart factory approach. There are parts of the integration that are pure product related, and through our collaboration with Siemens (Nordmeccanica has been selected by Siemens’ headquarters in Germany as one of 10 companies worldwide for the project “Global Acting OEM”), we are frontrunners in those developments. For those parts that are custom to factory integration, we do work side-by-side with our customers in providing those customizations needed to interact with existing realities. It is a fact that in every state or country that provides for incentives to the Industry 4.0 approach, our products always qualify for the highest ranking level.
Keller: Industry 4.0 is geared toward reducing waste and downtime; essential to a competitive operation. We’ve developed an Activ-check system to monitor machine health and activities, which directly impact productivity and waste. We want to be able to predict when a machine condition is deteriorating to anticipate a missed splice or transfer before it occurs. When we do that, we can correct the condition and avoid significant downtime when web loss occurs.
We hear that more and more converters are adding coating/laminating capability due to the high return on investment. Why is ROI so significant when it comes to this equipment?
Keller: When the material costs are such a significant part of your total cost, vertical integration makes economic sense. Generally speaking, savings are typically realized by bringing processes done by your supplier in-house. There are many factors that need to be explored before taking this step. Davis-Standard has the experience and global market knowledge to support customers in the decision-making process.
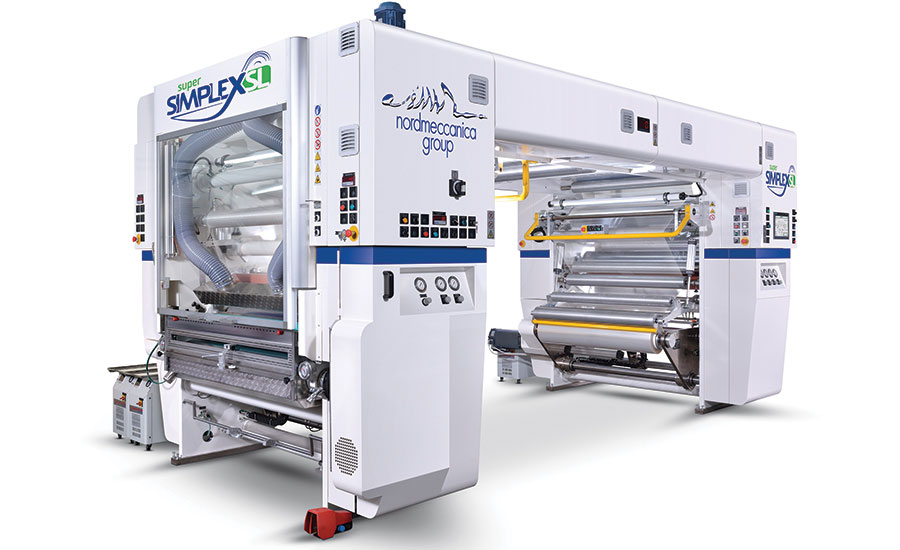
Caimmi: That is one of the best-kept secrets within the industry. ROI in coating and lamination is significantly faster versus every other capital equipment investment. Coating and lamination are the steps that allows differentiating the converted product from competition. Printing is a must-do, and every converter can provide printed webs. Instead it is the conversion stage (i.e., coating and lamination) that actually allows the product to perform. It is through the smart engineering of packaging design that final targets are achieved. And the engineering of packaging means the smart use of coating and lamination. Engineering the product at the lamination stage means the choice of the webs and the adhesive technology. The coating stage is then the one that is gaining importance based on the need to apply performance and finishing coatings (OPV, lacquers, barrier coatings, anti-fog, in register applications). The converter can, through the smart use of those technologies, implement the value of the products, therefore the margins and ultimately the ROI. ROI is always important. Once investing, ROI is the measurement unit of the quality of your investment – and honestly there is very few capital equipment that allow for less than one year of ROI, as in the case with some of our products.
Is there anything else you’d like to share about coating/laminating?
Keller: The coating/laminating markets demand machines capable of ever-increasing speeds, faster changeovers and minimal product waste. Many converters select low feature, inexpensive machines thinking they are ahead of the game, while their competitors select innovative, high-speed capable, low-waste machines. In the long-run, the latter results in dramatically lower operating costs, reduced scrap and a healthier bottom line.
Looking for a reprint of this article?
From high-res PDFs to custom plaques, order your copy today!