Flexible Packaging recently caught up with Gary Hughes, president and CEO of Brampton Engineering (BE), for a discussion ranging from sustainability in extrusion to current concerns about blown film equipment.
What’s new in extrusion equipment or technology? Do you plan on introducing anything new at NPE?
Hughes: Film producers are faced with the need to make more complex film structures with shorter job runs, which demands more flexible processes and highly repeatable extrusion systems. BE is excited to showcase the patent-pending Vector Air Ring, which offers a wider processing window and fully digital setup and process monitoring to ensure repeatable setups. When combined with the SCD 4.0 die technology, film producers have better-than-ever processes for producing better films.
With sustainability increasing in importance, how is extrusion equipment playing a role?
Hughes: We all know that when it comes to packaging, flexible formats dramatically reduce material usage over rigid packaging, typically 30 to 50 percent, and sometimes up to 80 percent by weight. This not only reduces the logistical impact of transporting empty and filled packages, but also the amount of waste to be disposed of. The high barrier capabilities of multi-layer films can extend product shelf life multiple times, reducing food waste, and in some applications, eliminate high energy refrigeration. Multi-layer extrusion equipment must be versatile to address challenging material combinations, whether reducing the percentage of difficult-to-recycle components or enabling post-consumer recycling, as resins unsuitable for food contact can be safely buried in a core layer.
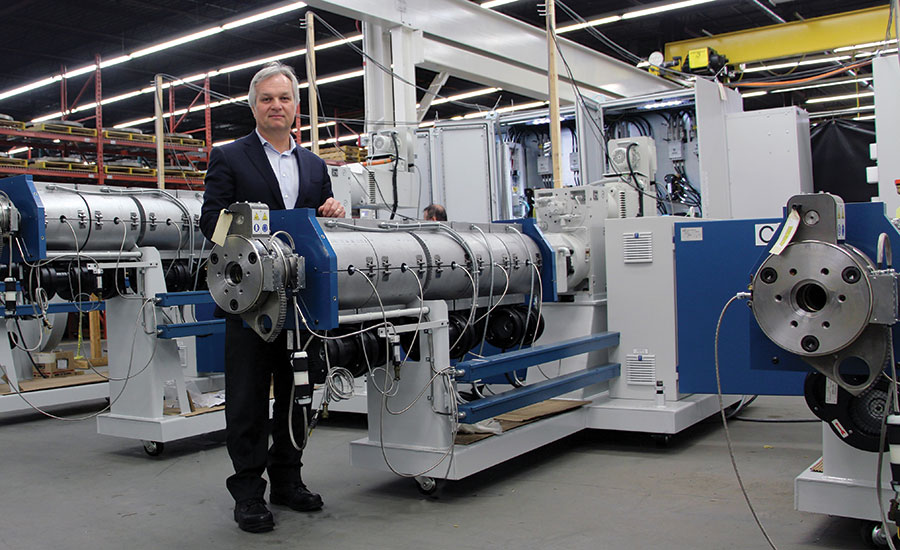
What types of developments/changes/trends do you foresee coming in the future?
Hughes: Film producers will continue to improve film quality and create more challenging film structures for more demanding applications while reducing costs. Sustainability will be an important influence on new applications and improvements on existing film structures. Versatility combined with repeatability will be increasingly demanded of blown film lines, rather than simply the highest output. Overall equipment effectiveness (OEE) across the portfolio of jobs encountered in today’s fast-paced operations will become a more important performance indicator. More automation, digital processes that are repeatable, and with more process expertise built into the systems is the future.
Is there anything that concerns you about the state of blown film extrusion equipment? What can be done to alleviate these concerns?
Hughes: In North America in particular, a lot of legacy film extrusion equipment is reaching the limits of its capability, particularly as films get more complex to address the needs of the markets, including the push to sustainability. However, the best route to improve an operation’s effectiveness is not always clear, simply because there are many pieces of equipment which have to perform in unison, and different film structures may have a variety of limiting factors preventing their successful extrusion on any particular line. So a holistic and open-minded approach to equipment audit and analysis of the operation’s future needs is required to recommend the best route – to upgrade the components limiting performance, to retrofit a line from 3 layers to 5, 7 or 9 layers, or to replace most or all of the line. Equipment suppliers who specialize in one component will naturally recommend upgrading that component. Suppliers who typically install complete lines may not have interest in helping a producer spread out their capital plan over several stages. BE offers complete lines, but a large fraction of our business is helping our customers to keep their existing equipment operating at top effectiveness.
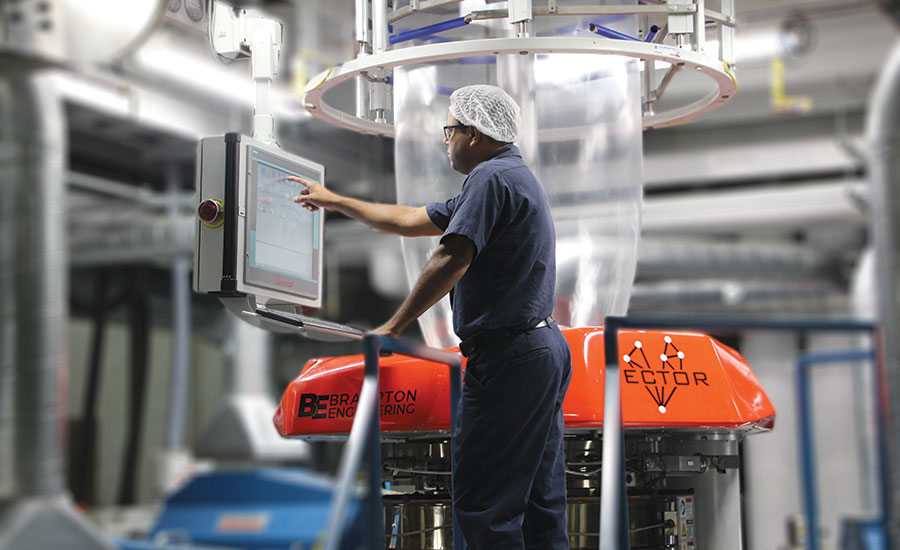
With blown film extrusion equipment as one of the more expensive investments a company will make, how do you communicate the value proposition of such purchases to your customers?
Hughes: Actually, blown film extrusion equipment is a small percentage of the cost of any film product. The majority is the polymer raw material, which is up to 80 percent of the cost of producing film. Therefore, investing in the most reliable, lowest cost to operate equipment, including lost time and scrap due to changeovers and maintenance, is critical to film producers’ competitive performance. BE focuses on providing technology features that are directly related to operational benefits and provide quantified payback or ROI justification. A good example is the retrofit Vector air ring or SCD 4.0 die onto existing lines. In many cases, our customers see payback in months – not years – from material saving and OEE improvements, while improving film quality for their customers.