Roundtable: Special Advertising Section
May 2018 Roundtable on Bag/Pouch Making

We sat down and discussed bag/pouch making with Timothy Lewis- CMD Corporation, Fabio Dacò- ELBA S.p.A., Jim Russell- Modern Manufacturing Services, LLC, Jesse Rosenow- Totani America, James F. Pease- Sun Centre USA, and Sanjay Amin- Mamata Enterprises, Inc..
Timothy Lewis
VP of Global Sales
CMD Corporation
24 years with the company
(800) 626-0210
www.cmd-corp.com
Fabio Dacò
Senior Sales Manager
ELBA S.p.A.
8 years with the company
+39 0331 305570
www.elba–spa.it
Jim Russell
President
Modern Manufacturing Services, LLC
9 years with the company
(585) 289-4261
www.modernmfg.net
Jesse Rosenow
Sales Engineer
Totani America
6 years with the company
(920) 632-7319
www.totaniamerica.com
James F. Pease
President/Owner
Sun Centre USA
14 years with the company
(224) 699-9058
www.suncentre.us
Sanjay Amin
General Manager-Sales; Marketing-Customer Support
Mamata Enterprises, Inc.
18 years with the company
(630) 801-2320
www.mamatausa.com
What’s new with your company when it comes to bag/pouch making?
Dacò: We are constantly striving to offer customers easy-to-use machines with fast changeover times and high flexibility. In these regards, we designed new solutions to collect the pouches and bags automatically.
Lewis: Our focus with equipment development, and our theme at NPE 2018 this month in Orlando, is: Technology that Empowers. CMD will exhibit for the first time at an NPE show the enhanced 0305GOWE Global Overlap Winder with even faster cycle rates for small count rolls, and a reliable and convenient bander/labeler that’s easy to position in or out, to offer the flexibility of banded or non-banded rolls. Collaborating with ExxonMobil and Sigma Plastics, CMD will convert bags with recycled content in our booth, W6271. Continuing the value of sustainability and consumer convenience, CMD will use and demonstrate the application of a new, easy-open roll label from CheMes M. Szperlinski.
Russell: Modern has introduced three new different levels of pouch making lines. The new pouch making lines cover the specific needs of the converters based on the pouch types and volumes they are producing. Our newest Momentum series line has been introduced to help with the new short run and digital printing requirements for today’s market. Our Velocity series machine covers the more conventional full featured pouch making requirements for customers that are running slightly higher volumes but are still looking for the flexibility to run multiple pouch sizes and configurations. Our latest Catalyst series model is a patented process that allows pouch making at high speeds with the added simplicity of changeovers.
Rosenow: Totani is always investing in new ideas and technologies. This is one of the key factors for our continuous growth and leadership in the industry. The old adage “be always ahead” continues to be one of our main values. Some examples of this philosophy are: TBRS technology for narrow web applications, Digital Positioning Assist technology and Quick Release seal bar tooling to reduce setup time, advanced sensor systems for automatic rejection of out of specification pouches to improve quality control and a high-speed die-cut system for shape pouches. Even the growth and success of the Box Pouch format is a true testament of Totani’s leadership in innovation.
Pease: Last year, we introduced our SCSP 600 Standup Pouch Machine, which has the ability to use one film to form standup pouches. Additionally, it can also make pouches with three films because of the upper roll and insert gusset feature. What makes this machine unique is that it comes standard with front and back registration so you can make standup pouches from two webs (using our unique tucking method) or insert a gusset if needed. This machine can also be upgraded with the CDA REDI-PAC system for inline thermal lamination so you can digitally print films and go directly to the pouch machine without adding steps, allowing you to make pouches all in one machine format.
We can also add the REDI-PAC thermal lamination system to our SCSG600 multi-format machine coupled with the Elplast or Zip-Pak cross web zipper applicator inline. This enables you to transform from pouches to rollstock with pre-applied zipper in the same machine.
Amin: With the increasing requirement for the ability to process and convert recyclable films, we have enhanced our capability to do so across our product range. Pouches, bags and sacks converted from PP woven fabric laminated with BOPP is a recyclable substrate. We have recently introduced a converting machine to convert such fabric into pouches and sacks. The machine does forming, back seam gluing, cutting, bottom-fold and stitching inline at extremely high speeds of up to 100 bags per minute. The machine is capable of producing 10 x 12-inch on smaller size and 24 x 40-inch on larger sizes.

Have new developments in printing technology enabling shorter runs impacted the requests your customers have when it comes to bag/pouch making equipment? How so?
Rosenow: Without a doubt, new printing technologies have enabled converters to employ shorter runs which, in turn, are having an important impact in customer requests for bag/pouch making equipment. These new technologies have already created new markets and areas of opportunities for pouch machinery manufacturers. Some of Totani’s innovations are a direct result of these new printing technologies.
Amin: New technology in printing has definitely changed the way converters are making pouches earlier. More often, changing market needs demand shorter job runs. To address these specific needs, we have a machine to help our customers address their needs for shorter job runs and quick changeovers. This machine has the shortest footprint in the industry and changeovers are under 30 minutes. Some of the highlighted features of this machine are: All servo seal stations allow you to control seal time and pressure precisely. Customers can achieve repeatable automatic changeovers in a matter of minutes due to motorized seal station movement, toolless changeover of seal tools/zipper tools, auto positioning of gusset punch holes depending on the format, auto positioning of film folding device depending on pouch size. It also allows facilities to do pre-open zippers allowing their co-packers and brand owners to run the pouches efficiently on their filling lines.
Pease: Of course everyone is always fighting for the large orders and turning away the 2,000 piece orders and so on. This is where we have lived for so many years, building the business around fast changeover and low scrap. Our customers want the most compact machine on the floor to produce pouches, which in turn allows them to have multiple machines for fast turnaround and have the capacity for the large orders. Our customers get the large orders that everyone wants because they can turn around in a cost effective manner the short runs no one wants to do.
Lewis: When we listened to the market during the research phase of our newest pouch system offering – the 760-SUP for standup pouches – the need to adapt and make money on short runs was a common complaint. As our interviews revealed, everyone says they have equipment that is quick to change over for short runs, but few prove it. And “short” is a relative term and only meaningful if backed by the data. Through our upfront investment in research and technology, our new machine design includes very smart, time-saving maintenance and operational features, and a provable, significant reduction in common changeover downtime compared with machines on the market today.
Russell: The short run and digital markets have driven the innovation and introduction of our Momentum series pouching line. With a small base footprint and intelligent servo sealing systems, this machine offers the quickest changeover in the industry. Modern has customers running these lines with as little as a few hundred pouches before they need to change to the next product, and no other line in the industry today is matching the simplicity of changeover along with the productivity of the Momentum series for today’s short-run pouching business.
Dacò: Our machines have been designed to allow customers to run short jobs thanks to the tool-less system for sealing dies and the fully automatic positioning system of each station. In this regard, we just anticipated customers’ needs.
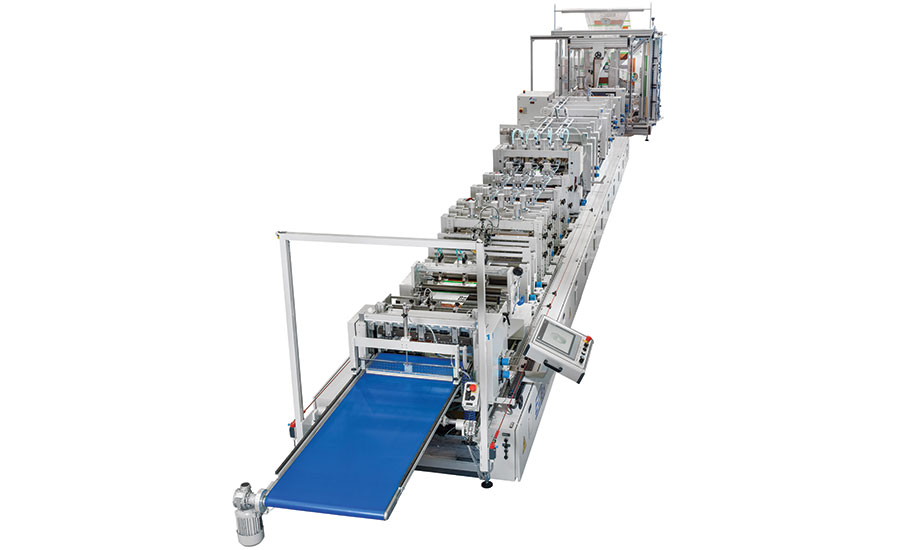
We’ve heard that the various different types of pouches are one of the keys driving growth in the market. Noting this, how important is it to have a versatile, flexible pouch machine?
Amin: One of the key issues/pain points for a buyer of pouch machines is to process a wide variety of film structures on the pouch machine besides flexibility to process a wide variety of pouch styles. Mamata’s unique seal technology allows customers to use a wide variety of films and make pouches. In fact, our customers have run a straight monolayer PE film to an 8 mil PE/nylon/PE structure and have made standup pouches. We can run laminated structures as well as co-ex recyclable unsupported PE structures and make a wide variety of pouches, be it three-side-seal, zipper, standup or even quad-seal pouches for pet food, fertilizers, etc.
Pease: Having a versatile pouch machine is key, being able to do only a few styles of pouches limits growth. Our customers want to do 2/3 side seal, standup pouch, twin lane standup pouch, side gusset, center seal and so many other formats, and in one machine like our SCSG600, this gives them the tool to get and keep business. The original thought process for so many machine manufacturers was to have a dedicated machine for a couple of style pouches, now the industry is forcing everyone to make a multi-format machine. This is the case, where the industry is driving the manufacturers of machines to follow. We have been making the SCSG 600 and 850 machines for the past 13 years in this format because we listened to our customers early.
Russell: There are many pouch uses and pouch configurations on the market today, so this leaves many factors and pouch uses that drive the market. If I had to only pick a couple, I would say the flat-bottom pouch and fitmented liquid pouches are still driving growth.
Dacò: It is extremely important as customers need to run short jobs and a variety of pouches on the same machine. Our SA-V 06 model has been designed to run two-side-seal, three-side-seal, Doypack, standup and side-gusset pouches (from one or more rolls) with a very short changeover time. This will allow the customer to face any new unpredictable market demand. Last but not least, the SA-V modular concept will allow the customer to update the machine by adding new features/modules without changing the existing structure. Once again, Elba anticipated customers’ needs in flexibility.
Rosenow: Versatility is high on the wish list for many small to medium sized converters. New converting opportunities don’t typically come in one type/size of package. Having the flexibility to create a 3SS, SUP or quad-seal pouch all on one asset greatly increases the value of that piece of machinery for any company. Now many may have a “jack of all trades, master of none” mentality when thinking of these kinds of versatile machines, but that is far from the case. While many of Totani’s machines are extremely versatile, there is never a sacrifice on quality to do so.
Lewis: We believe that equipment should be designed to put converters in control, to allow them to leverage skills and experience with advanced machine technology for long-term growth. Modular, upgradeable designs, including Industry 4.0-enabled equipment, allows predictive maintenance and helps put converters in control of their process by providing agility to configure their equipment for today’s market demands… and for tomorrow’s. Meaningful data analytics provided by sophisticated 4.0 technology allows pouch producers to dial in their process scientifically, so they control the sweet spot and the price point they can offer.
Aside from food and beverage, what markets are you seeing bag/pouch growth in? Is there a market that’s poised to become a big player moving forward?
Lewis: Likely most sectors will see growth, because the pouch offers an attractive supply chain cost proposition and lower environmental footprint. High-performance food, ready-to-eat baby food, and fruit compotes liquids, and household liquids and powders are all situated to grow. Categories will see a boost in growth with the continued commercialization of recyclable pouches.
Russell: It is hard to single out just one marketplace, but we are still seeing growth in the pet food markets and the agricultural-chemical markets. With more options for film structures and a wide bandwidth of accepted uses for pouches, these markets are seeing the benefits of pouching their products.
Pease: We have been working with DYMAPACK and developing the correct system for child-resistant pouch making. This market is wide open and this package delivers on what is needed, whether it is for the laundry/dishwashing pods to cannabis to medicine in pouches. We are seeing more and more people realizing a different package closure that works.
Amin: The major shift we see today is conversion from rigid packaging to flexible packaging, and this is going to be biggest potential in next 2-3 years. Also e-commerce is driving major changes in packaging.
Rosenow: Food and beverage still dominates the flexible packaging industry. Other strong markets include lawn and garden (seed, fertilizer, pest control), household chemicals (detergent, soap, pool chemicals) and tobacco to name a few. A fast riser in flexible packaging is the cannabis market. With the recent legalizations, many new products have been developed and most have chosen flexible packaging to get them to market.
Can you explain the one or two features of your bag/pouch making equipment that converters like the most?
Lewis: Fortunately, we stay in close contact with our customers, and in the last 18 months, have conducted several interview and survey projects to learn exactly what you are asking; what do our customers value about our equipment and CMD as a supplier? We have learned that we have scored high in several important areas, including: Being a partner to rely on for new technology, best-in-the-industry total production output, end product consistency and reliable support – service, parts, engineering and upgrades.
Rosenow: Totani’s Wait Time Feature allows seal quality setup at slow speed by inserting wait time. Once seals are set, the wait time is removed and high-speed production begins immediately with seals of identical quality, which saves material and decreases setup time. Additionally, Totani’s Print Smooth Function adjusts the film draw to maintain the film repeat so that tear notch position, corner cut position and side seals are not offset. Even if the print repeat is inaccurate, the film feed is uniform and is aligned with the pouch width.

Dacò: They like the possibility to have tailor-made solutions for their needs. Indeed, the modular concept of our SA-V model allows us to start from the product they need to manufacture, customizing the machine around it. This will allow them to have a machine that responds 100 percent to their needs, knowing that with new requests the machine can be updated accordingly. I would say that our customers like our approach to their needs and the customized solution our SA-V model can grant them the most.
Pease: Machine compact size and footprint means less time to setup and less scrap. Also, the front and back registration system with gusseting allowing the digital printing market and small printers to be able to make much larger pouches that normally only wide web printers could do.
Amin: One of the key features our customers like is processability of recyclable films along with laminates on our pouch machines. They also like our technology to control seal time and pressure digitally, allowing for more consistent and high-quality sealing.
Russell: The features converters like most about Modern’s machines is the flexibility and quick setup times. All of this is done through innovative engineering. Modern has introduced a new intelligent sealing system that allows the machine to run a more versatile product range by having variable cycle distances and electronic control over seal depth impression. These simple features allow the machine to run recyclable films that most pouch lines cannot produce.
Is there anything else you’d care to share about bag/pouch making?
Rosenow: Totani’s Box Pouch continues to provide an innovative solution to many packaging needs. This unique pouch, which the forming process is patented by Totani, has a flat, rectangular bottom and five printable surfaces for brand recognition. Recently, the FPA presented the Gold Award for Packaging Excellence and Sustainability, as well as the Silver Award for Expanding the Use of Flexible Packaging and Printing and Shelf Impact, to Totani Box Pouch partners. Congratulations to all!
Pease: Sun Centre USA Inc. has moved to a new location in Crystal Lake, Illinois. We opened this facility in order to better service our customers with our engineering and fabrication shop. We also have added our HSC 1300 slitter and our SCSP600 DR Redi-PAC machine so we can offer training for our customers and hands-on testing of new products in a controlled environment. We plan to have several open house training seminars in 2018.
Amin: Mamata is the only company that caters to both converters and end user packagers in this industry. We therefore understand what the basic process requirements are to make a pouch and the packaging requirements to fill a pouch. Our high-speed pre-made pouch filling system and our HFFS pouch system are ideal examples of this. Our unique ability to offer both pre-made pouch machines and end of the line packaging machines sets us apart.
Looking for a reprint of this article?
From high-res PDFs to custom plaques, order your copy today!