Silgan Closures Facility Receives Illinois Governor’s Sustainability Award
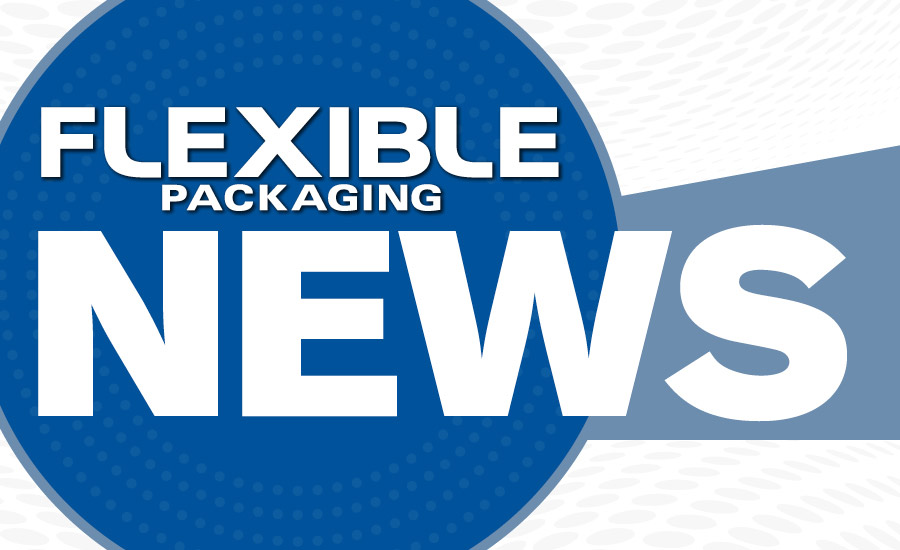
Silgan Closures’ manufacturing facility in Champaign, Illinois, has been awarded the 2017 Illinois Governor’s Sustainability Award, recognizing the plant’s efforts to improve safety, minimize waste, cut energy consumption and reduce emissions.
The Governor’s Award has been presented by the Illinois Sustainability Technology Center since 1987 to Illinois organizations that have demonstrated a commitment to sustaining Illinois’ environmental and economic health. Silgan Closures’ Champaign facility, which uses plastic resins to manufacture container closures, employs Lean Manufacturing practices, in addition to launching numerous in-house projects in 2016 to support the company’s goal of becoming more sustainable.
The first project involved moving from injection molding machines to compression molding machines. By making this switch, Silgan reduced cycle time and energy consumption. Since compression molding depends on a lower plastic extrusion temperature, less energy is needed to heat and cool the plastic resin. The new procedure allowed caps to be cooled quickly while still in the mold. These changes reduced greenhouse gas emissions by 2,891 metric tons.
The second project included leasing a train rail site near the facility to bring in resin by rail, rather than truck. Silgan made the switch because the volume of deliveries, traffic, driver availability and truck breakdowns often resulted in the facility receiving resin late or not at all. In making this change, the facility reduced the number of shipments, increased on-time delivery and reduced truck CO2 emissions by more than 2,500 metric tons per year.
Silgan also moved off-site warehousing on-site. The company had stored pallets of closures in off-site warehousing approximately one mile from the manufacturing plant. Pallets were moved from the warehouse to the manufacturing plant 27 times a week. Silgan decided to add additional warehouse space at the plant to eliminate the freight costs, risk of damage and longer lead times. In relocating inventory to the plant, the facility saved energy and transportation cost, improved quality control and reduced the operation’s emission footprint.
Furthermore, Silgan replaced existing T8 fluorescent lighting in the facility with LED lighting. The LED lights were designed to fit into existing light fixtures, eliminating the need for additional infrastructure. In addition to cost savings, the new lighting reduced the plant’s emission footprint, saving 136 tons of greenhouse gas emissions per year, and lamp waste up to 5 times that of ordinary T8 fluorescent lights.
Silgan continues to improve its good operating practices through maintenance scheduling, minimizing, resin changeovers and, on occasion, researching alternative services and technologies that will reduce the emissions and waste at the facility. For example, the Champaign facility has begun converting to more environmentally-friendly cleaning solutions and installed metering systems to control dispensing of these solutions. The facility also has its own plastic scrap recycling system on site to make scrap resin available to other organizations, eliminating scrap that would otherwise go to a landfill.
Silgan Closures
Looking for a reprint of this article?
From high-res PDFs to custom plaques, order your copy today!