Admiral Packaging Adds 10-Color Flexo Press to Increase Printing Capacity
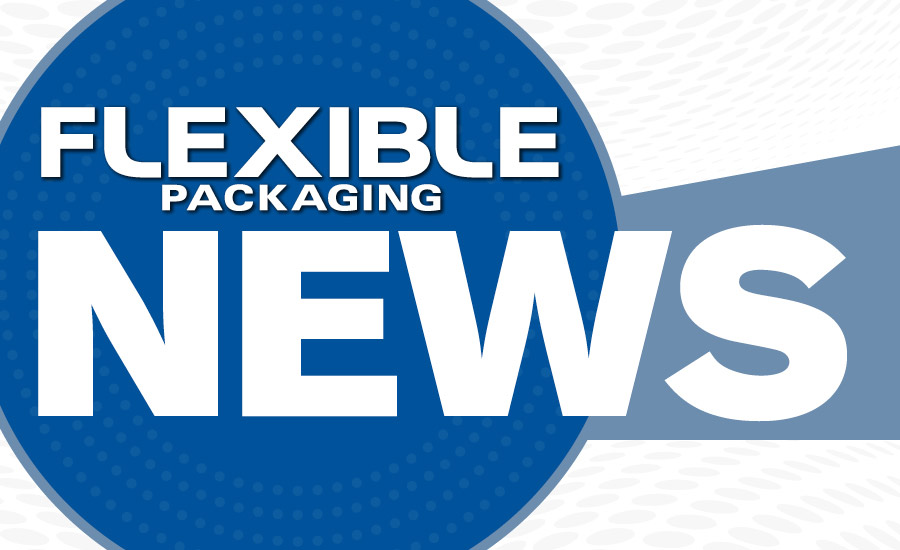
Admiral Packaging, a converter that produces a variety of products for general food packaging, has stepped up printing capacity with the addition of a 10-color MIRAFLEX C II flexographic printing press from Windmoeller & Hoelscher.
The new press joins a 10-color NOVOFLEX, also from W&H, and provides Admiral with greater flexibility of job management as well as the ability to get customers' jobs to market quicker. A new inset feature for second pass printing, such as matte finish and varnish applications, has opened new opportunities for both new and existing customers.
The MIRAFLEX II C was introduced at Drupa 2016, and the line at Admiral is the first in the U.S. It is equipped with W&H’s fully-integrated VISION web inspection system with defect check and color check as well as the color management system EASY-COL. These automation and assistance systems give the machine operator complete overview and control of the job on press. An additional feature on the new press is the award-winning TURBOCLEAN ADVANCED E inking and wash-up system with electric pulsation-free pumps, which will help Admiral cut down on energy and ink consumption.
Robert Hummell, Production Manager at Admiral, reports that the EASY modules and W&H VISION system help get a 10c job up and running at 1,500’ – 2,000’ fpm in just a few minutes. “There are a lot of great new features that make the new MIRAFLEX II easy to work with, allowing us to be more efficient and deliver great throughput to the rest of our operation.”
According to Admiral Vice President, John Wilbur, “We were looking to get the next generation of sophistication to provide the tools for us to reduce cycle times even further while increasing process rates. The MIRAFLEX II C fits nicely with Admiral’s Lean manufacturing culture. We will continue to identify waste and work tirelessly to remove it!”
Admiral Packaging
Looking for a reprint of this article?
From high-res PDFs to custom plaques, order your copy today!