Roundtable: Special Advertising Section
January/February 2017 Roundtable on Film Extruders
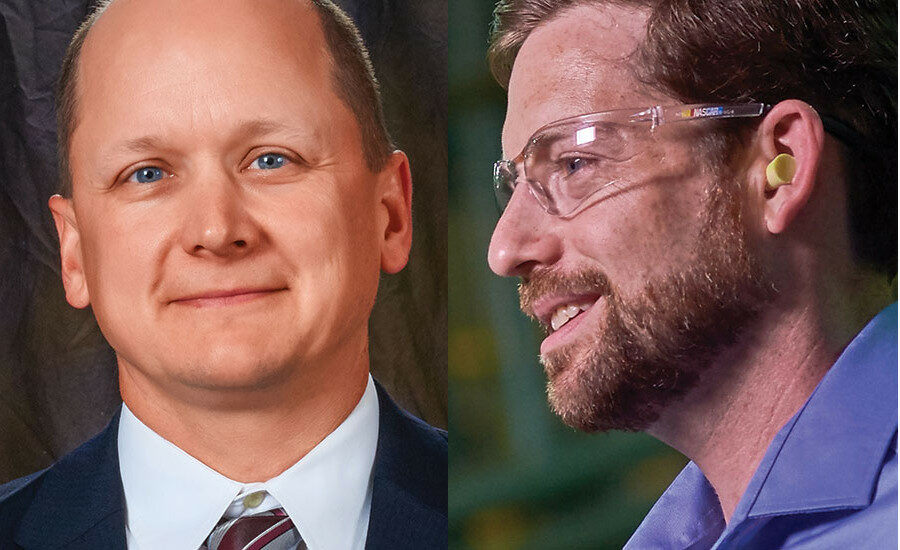
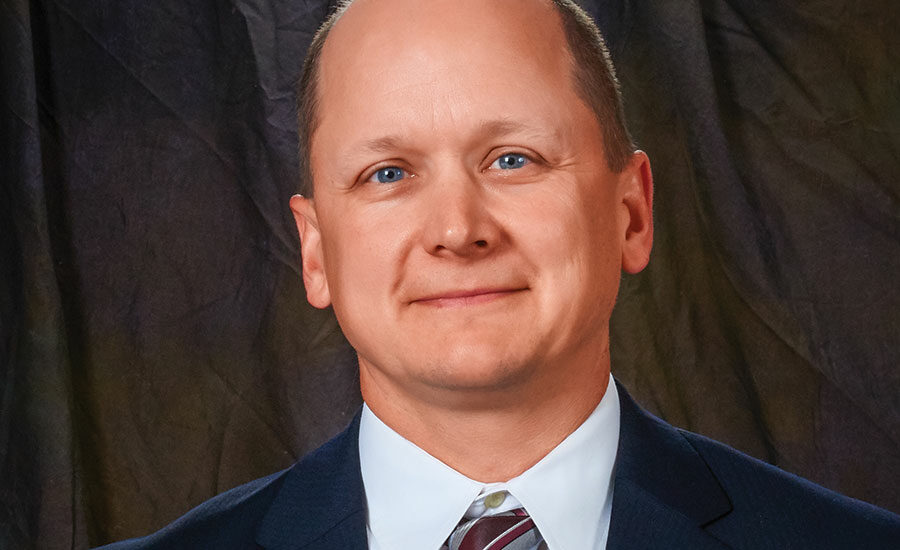
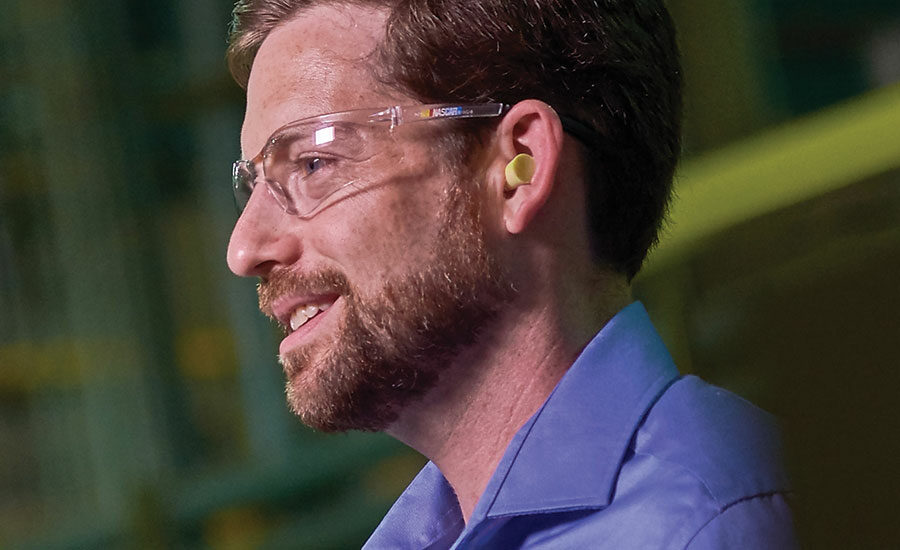



Eric Bender
Market Development Manager, New Platforms
Jindal Films Americas
15 years with the company
(800) 231-6577
www.jindalfilms.com
Eric Smith
Vice President of Technology
Charter NEX
18 years with the company
(877) 411-3456
www.charternex.com
Q: What’s new with your company or when it comes to film making? Did you release any new type(s) of films at PACK EXPO or any of the trade shows in 2016?
Bender: Jindal’s latest flexible packaging innovation, SealTOUGH, was launched at PACK EXPO 2016. SealTOUGH is a biaxially oriented polyolefin sealant film with 5,000 grams per inch of seal strength and improved clarity, puncture resistance and tensile strength over traditional blown PE sealant films, offering significant downgauging opportunities. Even with 40 percent downgauging, SealTOUGH provides a three-fold improvement in tensile strength, two-fold improvement in modulus, puncture resistance and impact resistance compared to the performance of traditional blown LLDPE sealant films.
Smith: Responding to the demand for more sustainable packaging options, Charter NEX introduced its line of GreenArrow recyclable multi-layer films at PACK EXPO 2016. The GreenArrow line of film products includes standalone films, sealant films and printable films. These recyclable multi-layer films offer the same convenience and functionality as multiple material structures, but have the added benefit of recyclability. Throughout 2016, Charter NEX increased its capacity by investing in multiple state-of-the-art extrusion lines. We remain committed to investing in the future, and in 2017 we will add additional blown film capacity and complete a corporate office expansion.
Q: What are some of the biggest factors that need to be considered by blown film extruders when creating either new or custom films?
Smith: First, understanding the requirements of the end-use application is essential. At Charter NEX, we have the ability to create a wide and complex range of films with unique performance properties. Through the use of engineered resins, our technical team designs each layer of a film solution to meet our customer’s film requirements and deliver characteristics such as barrier properties, seal performance, strength and tear properties. Second, the exchange of detailed project information with our customers is key to successful film design. Based on the product and how it is being packaged, our technical team will engineer a film solution to meet the properties and performance attributes required by the customer. The more collaboration we can have in the design stage about the performance required, the greater the success in new film development. When we can enhance an end-use package attribute, or satisfy a previously unmet need in an application, we have created a win-win for ourselves and our customer.
Q: What’s the most popular film (or type of film) that your company produces? What about the most unique film?
Bender: Jindal’s most popular product lines are its Bicor films that offer outstanding print performance, sealant performance and/or barrier performance using both co-extrusion and coating technology, and our Label-Lyte films, which deliver consistent, efficient, high-performance solutions to printers, converters and consumer goods companies for a wide range of labeling needs. In addition to SealTOUGH, Jindal’s most unique film is its Platinum Thermal 75PT600 film. It is a white polyolefin film that replaces both coated direct thermal (DT) substrates and thermal transfer ribbons (TTR). 75PT600 film provides outstanding printability using standard thermal and barcode printers and its chemical, heat and water-resistant surface makes it ideal for a number of indoor and outdoor applications. Platinum Thermal film can be used for pressure-sensitive labels, tickets and tags, and point-of-sale applications.
Smith: Today, 3-layer films are Charter NEX’s most popular product, however we continue to see the transition from 3-layer films to 5-layer films. With 5-layer films, customers have the ability to select a series of attributes that can be consolidated into one structure without compromising one attribute in favor of another. Each layer in the structure performs a specific function, adding benefit to the film. Charter NEX has been at the forefront of 5-layer innovation and development, and we continue to invest in state-of-the-art 5-layer extrusion equipment. Charter NEX is also known industry-wide for our ability to develop unique and innovative film solutions. We have designed and manufactured films for a wide variety of unique applications, including NASA’s scientific balloons, bulletproof vests and solar panels.
Q: What type of role has the increased focus on sustainability played in the research and development of film?
Smith: Charter NEX has always focused on sustainability. Our technical team works closely with top resin and additive suppliers to research and test new sustainable materials. We offer GreenArrow recyclable multi-layer films, ASTM D6400 compostable films and custom films using post-consumer recycled resins, various renewable resins and other sustainable materials. We also focus on source reduction. In many cases, by transitioning a customer to a co-extruded or 5-layer film, we are able to reduce the thickness of the film while increasing the film’s performance attributes.
Bender: Jindal Films pursues continuous efforts to understand and improve environmental performance across its operations and products based on sound science. Jindal Films is an active member of the Sustainable Packaging Coalition (SPC), and we are aware of and reacting to the latest trends and efforts around sustainability. A majority of our research and development efforts address one, if not multiple, aspects of the design objectives around packaging sustainability. Some examples include our SealTOUGH, Platinum Thermal and SuP film products. SealTOUGH addresses raw material source reduction and recyclability, and it has been approved by Trex for recycling. Platinum Thermal completely eliminates the need for thermal transfer ribbons. Jindal’s SuP product line is another recent technology development that addresses source reduction through the downgauging and replacement of thick PE sealant films in standup pouches.
Q: There’s been a lot of movement with flexible packaging beyond food and beverage to markets like pharmaceutical, health and beauty, and personal care markets. What are some considerations to keep in mind for film in this markets?
Smith: Advancements in film extrusion have accelerated in the past few years as suppliers of resin, equipment and other process inputs have introduced a variety of new products. Because of the volume in food and beverage applications, many of these advancements have been focused on these segments. However, Charter NEX has also increased its product versatility and its ability to handle smaller batch sizes, which supports the more specialized markets of pharmaceuticals, healthcare and personal care. Charter NEX utilizes world-class process controls, product and supply chain traceability and superior quality and documentation systems, all of which is necessary to meet the increasingly stringent manufacturing and quality regulations associated with the healthcare and pharmaceutical markets.
Looking for a reprint of this article?
From high-res PDFs to custom plaques, order your copy today!